Sensor Integrating Machine Elements: Difference between revisions
ReneGansel (talk | contribs) (→Data transfer: General Edit LoRaWAN) |
|||
Line 74: | Line 74: | ||
* Current lubrication regime | * Current lubrication regime | ||
==== | ==== Plain bearing ==== | ||
Besides roller bearings, plain bearings are the most frequently used machine elements in mechanical engineering, which enable the relative movements of machine parts to each other. A '''plain bearing''', or more commonly '''sliding contact bearing''' and '''slide bearing''', is the simplest type of bearing, comprising just a bearing surface and no rolling elements. Therefore, the journal (i.e., the part of the shaft in contact with the bearing) slides over the bearing surface. The simplest example of a plain bearing is a shaft rotating in a hole. The effects of bearing damage are serious in economic terms as well as in terms of safety. Consequently, condition monitoring of bearings is becoming increasingly important to minimize the downtime. Plain bearings are characterized by having a longer service lifetime and higher load capacity at equivalent dimensioning compared to roller bearings (Lau et al. 2012). Therefore, plain bearings are especially suitable for long-term and heavy-duty applications. Accordingly, roller bearings are increasingly being replaced by plain bearings in the planetary stages of wind turbine gearboxes (Ni 2022). Additionally, first concepts of main drive trains with plain bearings in wind turbines have been published (Jonuschies 2015; Rolink et al. 2020). In summary, significant challenges for the safe and economical operation of a drive train can be identified: The severe effects of bearing damage in drive train systems and the current development trends leading to higher loads and increased use of plain bearings in drive trains. | |||
Regarding the type and direction of the forces occurring between the moving machine elements, a distinction is drawn between statically or dynamically loaded radial and axial plain bearings (Sauer 2018). Furthermore, a distinction between plain bearings without the use of an intermediate medium, which are permanently subject to wear, and those with a separating medium (typically oil) can be made. Plain bearings using a separating medium are advantageous in terms of their friction behavior, which can be optimized to the extent of no wear occurring during operation (Hinzen 2022). However, the wear-free state can only be ensured if solid contact between the two contact partners, the bearing bush and the shaft, is completely avoided. Plain bearings, which are operated using a separating medium and therefore can enable wear-free operation, are classified into hydrostatic and hydrodynamic plain bearings. In case of hydrostatic plain bearings, the wear-free state is achieved by applying pressure to the lubricating film externally by a pump. Therefore, the state of motion created, does not influence the separation of the surfaces relative to each other. In the case of hydrostatic plain bearings, the lubrication gap height can be controlled by using active hydraulic chamber systems (Althaus 1991; Santos 2011; Kurth et al. 2019). Due to active separation of the wear surfaces, sensor-integrated condition monitoring is of secondary relevance for hydrostatic plain bearings. The friction and wear behavior of the surfaces moving relative to each other in hydrodynamic plain bearing is decisively dependent on their relative speed. Wear-free conditions are only achieved at sufficient relative speed. Hydrodynamic axial plain bearings, which primarily support axial forces in the direction of the shaft, are used less frequently compared to radial hydrodynamic plain bearings. Accordingly, the following section will focus primarily on hydrodynamic radial plain bearings and the possibilities for condition monitoring. | |||
For monitoring hydrodynamic radial plain bearings, the measurement of a number of quantities is well established. Possibly used monitoring principles are: | |||
* Temperature Monitoring | |||
* Acoustic Emission | |||
* Lubricant monitoring | |||
* Friction torque | |||
* Orbital analysis | |||
* Electric contact resistance | |||
* Acceleration monitoring | |||
==== Shaft coupling ==== | ==== Shaft coupling ==== |
Revision as of 14:22, 16 May 2024
Your first time working with this wiki? Please read Getting started first!
Interaction of sensor system and machine element
Exemplary measurement tasks in machine elements
Gear
Gears are usually subject to a standardized design process (ISO6336), with a variety of power levels (e.g., wrist watches to wind turbines). Since gears are relevant for the functionality of the overall system, detecting gear faults as early as possible is benefitial. The physical quantities relevant for the primary function are:
- instantaneous rotational speed
- torque
- temperature
- exitation behaviour
Other physical quantities include:
- type of lubrication
- lubrication quality
- gear material
- gear geometry
Thus, for an efficient monitoring of gears the following physical quantities are beneficial to record:
- torsional acceleration
- lubrication thinkness in the loaded contact
- instantaneous rotational speed
- gear temperature
- structure borne noise
Bolt
Standardized metrical bolts according to ISO 4014 are the most widely used machine elements. Thus they offer excellent potential for driving digitalisation through the procurement of data. Therefore, in addition to recording physical quantities that are directly related to the primary function, it is also possible to record a range of other physical quantities. The physical quantities relevant for the primary function are:
- axial force
- torque
- bending torque
Other physical quantities that can be recorded include:
- temperature
- acceleration
- rotational speed
- electric field
- magnetic field
To integrate sensors into the screw/bolt as required by the boundary conditions of the SPP2305 to maintain the mechanical interfaces, the sensors and electronics usually need to be integrated into the structure. This harms the mechanical function of the screw.
Rolling bearing
Rolling bearings play a central role in the world of machine elements. These inconspicuous yet extremely vital components are indispensable in a wide range of industrial applications, whether in automotive drive systems, wind turbines, huge turbines in power plants or in the precise mechanisms of state-of-the-art robot technology. Rolling bearings enable low-friction movement and transmit forces efficiently, making a significant contribution to the performance and reliability of a wide range of machines.
As digitalization progresses, the integration of digital technologies in a rolling bearing opens up new possibilities for monitoring and optimization. By implementing condition monitoring systems, data can be collected, analyzed and interpreted during operation to monitor the condition of a rolling bearing in real time.
These systems use a variety of sensors to record parameters such as temperature, vibration, lubricant condition and load. In particular, the use of thin-film sensors on the bearing disk of a rolling bearing can be used to detect temperatures or acting forces directly in the effective zone of the bearing. The collected data is then evaluated using algorithms and analysis techniques to detect potential anomalies or deviations from normal operation at an early stage. This allows maintenance intervals to be optimized, downtimes to be minimized and preventive maintenance measures to be planned.
Physical parameters that can be measured:
- Temperature
- Strain
- Rotational speed
The condition monitoring of rolling bearings is therefore a key element in the predictive maintenance of machines and systems. It enables a proactive approach to maintenance by providing operators and engineers with important insights into the current condition of the bearings. By detecting wear, damage or other problems in good time, expensive repairs can be avoided and the service life of the machines can be extended. In an increasingly digitalized world, condition monitoring therefore plays a crucial role in ensuring the efficiency, reliability and cost-effectiveness of industrial processes.
Gas foil bearing
Gas foil bearings (GFBs) are an advanced class of fluid dynamic bearings that utilize a thin layer of gas, typically air, as a lubricant in a gap between a rotating journal and an elastic metal foil structure, consisting typically of a supporting bump foil and a smooth top foil. This design allows for the creation of a load-bearing gas film at operational speeds, effectively minimizing friction and wear by maintaining separation between the rotor and bearing surfaces through dynamic pressure in the lubrication film. The compliant foil structure enables adaptability to varying operational conditions without the need for tight radial clearances. GFBs are thus able to function at large rotating speeds with high efficiency, low maintenance and without oil and related problems. GFBs are thus particularly suited for applications in high-speed rotating machinery where oil lubrication is undesirable or impractical, including but not limited to fuel cell blowers, air cycle machines, microturbines, and compact compressors.
Despite their advantages, GFBs can be susceptible to strong subharmonic vibrations, similar to those encountered in other hydrodynamic bearings. In addition, they may suffer from thermal instability, leading to unstable operation due to the different thermal expansion of different GFB components. The integration of sensors within GFBs for real-time monitoring of operational conditions will allow controllers to better adress these challenges. The most relevant measurement quantities in this regard include:
- Vibrations
- Temperature (fields) in bearing components and gas film
- Location of the rotor
Further quantities that may be deduced or measured within a GFB include:
- Pressure (fields) in the gas film
- Gas composition, water content
- Rotational velocity of the rotor
- Orbit of the rotor
- Current lubrication regime
Plain bearing
Besides roller bearings, plain bearings are the most frequently used machine elements in mechanical engineering, which enable the relative movements of machine parts to each other. A plain bearing, or more commonly sliding contact bearing and slide bearing, is the simplest type of bearing, comprising just a bearing surface and no rolling elements. Therefore, the journal (i.e., the part of the shaft in contact with the bearing) slides over the bearing surface. The simplest example of a plain bearing is a shaft rotating in a hole. The effects of bearing damage are serious in economic terms as well as in terms of safety. Consequently, condition monitoring of bearings is becoming increasingly important to minimize the downtime. Plain bearings are characterized by having a longer service lifetime and higher load capacity at equivalent dimensioning compared to roller bearings (Lau et al. 2012). Therefore, plain bearings are especially suitable for long-term and heavy-duty applications. Accordingly, roller bearings are increasingly being replaced by plain bearings in the planetary stages of wind turbine gearboxes (Ni 2022). Additionally, first concepts of main drive trains with plain bearings in wind turbines have been published (Jonuschies 2015; Rolink et al. 2020). In summary, significant challenges for the safe and economical operation of a drive train can be identified: The severe effects of bearing damage in drive train systems and the current development trends leading to higher loads and increased use of plain bearings in drive trains.
Regarding the type and direction of the forces occurring between the moving machine elements, a distinction is drawn between statically or dynamically loaded radial and axial plain bearings (Sauer 2018). Furthermore, a distinction between plain bearings without the use of an intermediate medium, which are permanently subject to wear, and those with a separating medium (typically oil) can be made. Plain bearings using a separating medium are advantageous in terms of their friction behavior, which can be optimized to the extent of no wear occurring during operation (Hinzen 2022). However, the wear-free state can only be ensured if solid contact between the two contact partners, the bearing bush and the shaft, is completely avoided. Plain bearings, which are operated using a separating medium and therefore can enable wear-free operation, are classified into hydrostatic and hydrodynamic plain bearings. In case of hydrostatic plain bearings, the wear-free state is achieved by applying pressure to the lubricating film externally by a pump. Therefore, the state of motion created, does not influence the separation of the surfaces relative to each other. In the case of hydrostatic plain bearings, the lubrication gap height can be controlled by using active hydraulic chamber systems (Althaus 1991; Santos 2011; Kurth et al. 2019). Due to active separation of the wear surfaces, sensor-integrated condition monitoring is of secondary relevance for hydrostatic plain bearings. The friction and wear behavior of the surfaces moving relative to each other in hydrodynamic plain bearing is decisively dependent on their relative speed. Wear-free conditions are only achieved at sufficient relative speed. Hydrodynamic axial plain bearings, which primarily support axial forces in the direction of the shaft, are used less frequently compared to radial hydrodynamic plain bearings. Accordingly, the following section will focus primarily on hydrodynamic radial plain bearings and the possibilities for condition monitoring.
For monitoring hydrodynamic radial plain bearings, the measurement of a number of quantities is well established. Possibly used monitoring principles are:
- Temperature Monitoring
- Acoustic Emission
- Lubricant monitoring
- Friction torque
- Orbital analysis
- Electric contact resistance
- Acceleration monitoring
Shaft coupling
"Couplings are mechanical elements that connect two shafts in order to transmit mechanical power from one to the other. Furthermore, they i) can compensate for shaft misalignment, ii) have a switching function to interrupt or limit the power flow, and iii) compensate for shocks. The industry provides a variety of application-specific design, which satisfy diverse requirement profiles. VDI 2240 provides a suitable basis for selecting and classifying couplings according to their requirements. A subdivision is made according to switchable (clutch) and non-switchable (couplings) couplings. Based on this classification, different possible measurement quantities result. For couplings, the measured variables of a torque and rotational speed are particularly relevant. Furthermore, temperature, wear, shaft misalignments, restoring and reaction forces, and vibrations can be significant. For clutches, which also includes brakes, the measurement of the same parameters is desirable. Additionally, relevant parameters are clutch engagement and slip between the two hubs." [1]
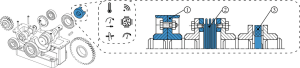
Important features that are of interest for these machine elements are:
- Torque,
- Rotational speed,
- Temperature,
- Shaft misalignment and
- Vibration
An important subclass of couplings are elastic couplings such as jaw couplings. They can be used to compensate for shaft misalignments and can mitigate critical torque shocks. Couplings are ideal components for measuring process data as they are located directly in the power flow.
Splined shaft
Splined shafts are a shaft-hub connection which are used to transmit torque. Important features that are of interest for these machine elements are:
- Torque
- Rotational speed
- Temperature
Key
Seal
Calculation methodology for service life / load carrying capacity
Evaluation method for load carrying capacity
Mechanical integration
Prototypes
In order to test the developed concept it is important to start with the production of prototpyes as early as possible to gain a better understanding and to mitigate or even detect the amount of possible failure modes. In this way, possible errors that were not previously thought of can be identified.
Components
Wiring / connectors
When cables are used inside a machine element they are subjected to´(i) cyclic strains or (ii) very high strains and stresses. It follows that they often break down. In order to eleviate this problem, micro coaxial cables can be used.
Testing / validation
Requirements for test technology
Validation strategy
Cost aspects
Potentials / challenges additive manufacturing
Potentials / challenges heat treatment
Operating strategy
Data handling
Algorithms for reduction
Methods for buffering
Outlook on the use of data
Operating strategy for processors
Validation strategy
Data transfer
Barriers / shielding
Protocols
- Bluetooth Low Energy
- Zigbee
- LoRaWan
Long Range Wide Area Network (LoRaWAN) is a low-power wireless network protocol operating at the network layer. It is defined by the LoRa Alliance and provides specifications that are freely available. Additionally, software building blocks are accessible as open-source software.
The architecture of LoRaWAN is star-shaped. LoRa end devices communicate with LoRa gateways, which then forward the data packets to a LoRaWAN server. This server interfaces with IoT platforms and applications. Communication within LoRaWAN is doubly encrypted using 128-bit AES, both from the end device to the network server and from the network server to the application server.
LoRa end devices and gateways in LoRaWAN utilize a proprietary and patented transmission method based on a chirp spread spectrum modulation technique called “LoRa". LoRa operates at the physical layer and is asymmetrically designed for energy efficiency, achieving uplink communication ranges of over 10 km. Data rates range from 292 bit/s to 50 kbit/s. Various operational modes, including quasi-continuous downlink communication, are possible, although the latter affects energy efficiency. The LoRa Alliance also refers to this technology as Low Power Wide Area Networks (LPWANs). LoRa uses different regional frequency bands in the ISM and SRD bands. For example, in Europe, the frequency band ranges from 433.05 to 434.79 MHz (ISM Band Region 1) and from 863 to 870 MHz (SRD Band Europe). The coverage extends from 2 km in urban areas to 40 km in rural regions. Notably, LoRa’s penetration capabilities allow it to reach even basement areas [2].
- Mioty
- Sigfox
- NB-IOT
Microsystem technology
Sensor systems
Overview of physical measuring principles
Temperature
Strain
Strain can be measured in two ways:
- Strain gauges
- Piezo elements
Acceleration
Acoustic noise
Conductivity / impedance
One way of measuring large strains is to use dielectric elastomer sensors (DES) [3]. They consist out of a dielectric layer which is sandwiched between two compliant electrodes. An electric field will form if an electric potential difference is applied on the two electrodes and a capacitance can be measured. Electrically, DES behave like plate capacitors. A deformation of the DES leads to a change in the capacitance which can then be used to measure the strain or force which caused this deformation.
Resilience
Energy harvesters
Different types of energy harvesters can be used to extract energy from the environment. Typical energy harvesters are:
Piezoelectric energy harvesting
Thermoelectric energy harvesting
Electrostatic energy
Electromagnetic energy harvesting
Radiofrequency energy harvesting
Energy storages
Processors (in situ)
Methodology for design of SiME
SiME can be understood as mechatronic or cyber-physical systems (CPS) due to their mechanical, electrical and information technology components. The development of mechatronic systems can be methodically supported. The VDI guideline VDI2206 for the design of mechatronic systems uses the V-model as a central development tool. In the V-model, discipline-specific solutions are developed based on the requirements and checked through verification and validation activities in the form of tests and simulations. A V-model adapted to the development of modular product architectures can be seen in Fig. ##.
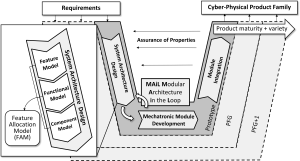
Modular system
The idea of a modular system is to be able to create products by combining modules. For SiME, this means being able to create application-specific system configurations of microelectronic components and modules for sensor systems for SiME with minimal effort. Depending on the ME and application, suitable components and modules are selected and configured into a compatible overall system, which is then integrated into the respective ME in a space-neutral manner without impairing the primary function.
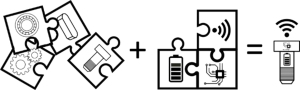
Figure ## shows this schematically by equipping various ME such as a gear wheel, ball bearing, screw or feather key with an integrated sensor system and thus becoming a SiME. The sensor systems require basic modules for their functionality to fulfill their respective measuring task, suitable data processing and successful energy management.
A methodical procedure for developing a configurable modular system is shown schematically in Fig. ##. The procedure mainly consists of a data input and two associated methods. Method 1 describes the implementation of product architectures in SysML. Method 2 describes the functionality of the configuration system. Here, individual product variants are generated on the basis of the various product architecture alternatives.
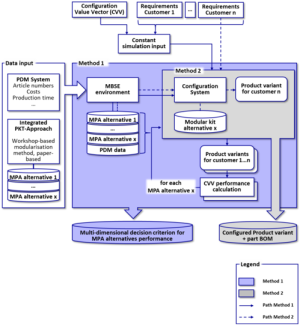
Configuration network diagrams are created for system synthesis. The product properties are linked to the components and the components are assigned to the respective modules. The overall structure can then be implemented in SysML.
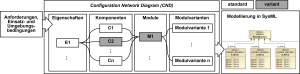
In SysML, individual diagrams can be created separately, which are arranged along the V-model as shown here. Different diagram types can be used in SysML, such as requirement or block diagrams, in which the product properties, components, modules and module variants can be mapped. The individual diagrams can be linked by dependency matrices. In this case, requirements are linked to product properties, properties to components, components to modules and modules to module variants. An exemplary hierarchical requirements diagram is shown in Fig. ##.
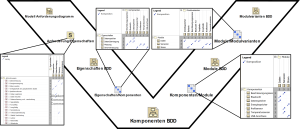
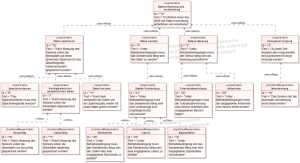
Costs of electronic components
High-quality
Low-quality
Literature
- ↑ Kirchner, E., Wallmersperger, T., Gwosch, T., Menning, J. D., Peters, J., Breimann, R., ... & Stahl, K. (2024). A Review on Sensor‐Integrating Machine Elements. Advanced Sensor Research, 3(4), 2300113.
- ↑ https://www.lora-wan.de/
- ↑ Rosset, S., & Shea, H. R. (2016). Small, fast, and tough: Shrinking down integrated elastomer transducers. Applied Physics Reviews, 3(3)