Sensor Integrating Machine Elements: Difference between revisions
(66 intermediate revisions by 14 users not shown) | |||
Line 1: | Line 1: | ||
== Introduction == | == Introduction == | ||
Caused by Industry 4.0 and the implementation of cyber-physical systems, a significant | Caused by Industry 4.0 and the implementation of cyber-physical systems, a significant demand for high-quality and reliable information about relevant state and process variables of technical systems arises. Sensor-integrating machine elements (SiME) offer great potential in this context since they enable the measurement of these variables directly at or close to their point of origin, so-called in-situ measurement. SiME build upon the primary mechanical functions of conventional machine elements and extend them by sensory functions. For SiME, the measurand - the quantity to be measured - is directly affected by the primary mechanical function of the machine element and measured by integrated sensors. Since the interfaces of the conventional machine elements are maintained and almost no additional installation space is required, SiME can easily be retrofitted into technical systems that were not developed against today's background. This means that also older technical systems can be made usable and continue to be operated in the context of Industry 4.0, which is particularly advantageous from an ecological point of view.<ref name="Kirchner2024" /><ref name="Welzbacher2021" /> | ||
Consequently, | Consequently, SiME can pave the way for widespread digitalization. However, to fulfill this vision, a varity of new and innovative SiME are needed. Therefore, the German Research Foundation (dt. Deutsche Forschungsgemeinschaft, DFG) funded the priority program (dt. Schwerpunktprogramm, SPP) 2305. The goal of the SPP is the development of various SiME. In the following, the results and findings of the ten projects conducted within the SPP 2305 are outlined in the form of a wiki. The projects of the SPP 2305 are: | ||
* Auto-informative plain bearings | * [https://gepris.dfg.de/gepris/projekt/466775494?language=en Auto-informative plain bearings] | ||
* Elastic couplings with integrated flexible dielectric elastomer sensors | * [https://gepris.dfg.de/gepris/projekt/466661922 Elastic couplings with integrated flexible dielectric elastomer sensors] | ||
* Integrated sensors for intelligent large-size bearings | * [https://gepris.dfg.de/gepris/projekt/466778958 Integrated sensors for intelligent large-size bearings] | ||
* Load sensitive | * [https://gepris.dfg.de/gepris/projekt/466760574 Load sensitive splined shaft with sensory material] | ||
* Microelectronic modular system for sensor-integrating machine elements | * [https://gepris.dfg.de/gepris/projekt/466493340 Microelectronic modular system for sensor-integrating machine elements] | ||
* Sensor-integrating machine element radial shaft seal for monitoring of operation conditions and lubricant quality | * [https://gepris.dfg.de/gepris/projekt/466192751 Sensor-integrating machine element radial shaft seal for monitoring of operation conditions and lubricant quality] | ||
* Sensor-integrating feather keys for the detection of torques | * [https://gepris.dfg.de/gepris/projekt/466657550 Sensor-integrating feather keys for the detection of torques] | ||
* Sensor-integrating gear | * [https://gepris.dfg.de/gepris/projekt/466653706 Sensor-integrating gear] | ||
* Sensor-integrating bolts for multiaxial force measurement and derivation of a design methodology for sensor integration in closed cylindrical machine elements | * [https://gepris.dfg.de/gepris/projekt/466650813 Sensor-integrating bolts for multiaxial force measurement and derivation of a design methodology for sensor integration in closed cylindrical machine elements] | ||
* Standardized integral instrumentation of gas foil bearings for condition and operation monitoring | * [https://gepris.dfg.de/gepris/projekt/466782279 Standardized integral instrumentation of gas foil bearings for condition and operation monitoring] | ||
== Exemplary measurement tasks in machine elements == | == Exemplary measurement tasks in machine elements == | ||
In the following, exemplary measurement tasks and their respective quantities of interest are described for the machine elements that are considered in the respective projects within the SPP 2305. | |||
==== Gear ==== | ==== Gear ==== | ||
Gears are usually subject to a standardized design process ( | Gears are usually subject to a standardized design process (ISO 6336<ref>International Organization for Standardization (2019, November 1). ''Calculation of load capacity of spur and helical gears'' (ISO 6336). Beuth.</ref>), with a variety of power levels (e.g., wrist watches to wind turbines). Since gears are relevant for the functionality of the overall system, detecting gear faults as early as possible is benefitial. A measurement at or in the gear is of interest because of the damping of the elements from the gear to the housing, which is the typical measurement position. | ||
The physical quantities relevant for the primary function are: | [[File:DMK-SIZA.jpg|thumb|Sensor integrating gear wheel according to Knoll et al.<ref>Knoll, E., Rothemund, M., Otto, M., Rupprecht, B., Ochs, M., Vogel-Heuser, B., Brederlow, R., & Stahl, K. (2024). Evaluation of vibration behavior at different sensing positions on gearboxes. ''Forschung Im Ingenieurwesen'', ''88''(1). <nowiki>https://doi.org/10.1007/s10010-024-00750-6</nowiki></ref> - CC BY 4.0]] | ||
The physical quantities relevant for the primary function of the gear operation are: | |||
* instantaneous rotational speed | * instantaneous rotational speed | ||
* torque | * torque | ||
* temperature | * temperature | ||
* | * excitation behaviour | ||
Other physical quantities include: | Other relevant physical quantities include: | ||
* type of lubrication | * type of lubrication | ||
* lubrication quality | * lubrication quality | ||
* gear material | * gear material | ||
* gear geometry | * gear geometry | ||
Thus, for an efficient monitoring of gears the following physical quantities are beneficial to | Thus, for an efficient monitoring of gears the following physical quantities are beneficial to be measured: | ||
* torsional acceleration | * torsional acceleration<ref>Binder, M., Stapff, V., Heinig, A., Schmitt, M., Seidel, C., & Reinhart, G. (2022). Additive manufacturing of a passive, sensor-monitored 16MnCr5 steel gear incorporating a wireless signal transmission system. ''Procedia CIRP'', ''107'', 505–510. <nowiki>https://doi.org/10.1016/j.procir.2022.05.016</nowiki> </ref><ref name=":1">Hasenoehrl, S., Peters, J., & Matthiesen, S. (2024). Integration of Sensors for Enhanced Condition Monitoring in Polymer Gears: A Comparative Study of Acceleration and Temperature Sensors. ''Applied Sciences'', ''14''(6), 2240. <nowiki>https://doi.org/10.3390/app14062240</nowiki></ref><ref name=":3">Knoll, E., Rupprecht, B., Groppo, E., Otto, M., Vogel-Heuser, B., Brederlow, R., & Stahl, K. (2023). MODULAR EXTENSION OF FZG-GEAR TEST RIG FOR IN-SITU MEASUREMENT POSSIBILITIES. In IIAV CZECH s.r.o. (Chair), ''29th International Congress on Sound and Vibration.'' Symposium conducted at the meeting of IIAV CZECH s.r.o., Prag.</ref><ref>Peters, J., Ott, L., Dörr, M., Gwosch, T., & Matthiesen, S. (2021a). Design of sensor integrating gears: methodical development, integration and verification of an in-Situ MEMS sensor system. ''Procedia CIRP'', ''100'', 672–677. <nowiki>https://doi.org/10.1016/j.procir.2021.05.142</nowiki></ref><ref>Peters, J., Ott, L., Dörr, M., Gwosch, T., & Matthiesen, S. (2021b). Sensor-integrating gears: wear detection by in-situ MEMS acceleration sensors. ''Forschung Im Ingenieurwesen.'' Advance online publication. <nowiki>https://doi.org/10.1007/s10010-021-00575-7</nowiki></ref> | ||
* lubrication | * lubrication thickness in the loaded contact | ||
* instantaneous rotational speed | * instantaneous rotational speed | ||
* gear temperature | * gear temperature<ref name=":1" /><ref name=":3" /> | ||
* structure borne noise | * structure borne noise | ||
Depending on the assembly into the gearbox and the type of gear (spur gear or helical gear) different designs are possible which are also depending on classical designs of microelectronic circuits. So, for gears the following two designs are most relevant: | |||
* circuit board on the side plane of the gear | |||
* axial cavities (possible for helical and spur gears, better suited when press fit is used instead of feather key, more interaction with mechanical operation of the gear) | |||
==== Bolt ==== | ==== Bolt ==== | ||
Standardized metrical bolts according to ISO 4014 are the most widely used machine elements. Positioned in the load path, they offer excellent potential for driving | [[File:SiS in gearbox.png|alt=Bolts in a generic gearbox|thumb|418x418px|Bolts in a generic gearbox, source: [https://onlinelibrary.wiley.com/doi/10.1002/adsr.202300113 Kirchner et al. 2023]]] | ||
Standardized metrical bolts according to ISO 4014 and dimensioned according to VDI 2230 are the most widely used machine elements. Positioned in the load path, they offer excellent potential for driving digitalization through the procurement of in-situ data. Therefore, in addition to measure physical quantities that are directly related to the primary function, it is also possible to measure a range of other physical quantities. The physical quantities relevant for the primary function are: | |||
* torque (from tightening) | |||
* axial force | * axial force | ||
* bending torque | |||
* bending torque | |||
Other physical quantities that can be | Other physical quantities that can be measured include: | ||
* temperature | * temperature | ||
* acceleration | * acceleration | ||
Sensor-integrating bolts exist in the state of the art, e.g. the following: | |||
The integration of sensors and electronics for energy delivery and processing requires sufficient design space inside the bolt. Any removal of material does however weaken the primary function. | * [https://consenses.de/produkte/sensoren/kraft-und-vibrationssensoren/piezobolt-pb20/produkt PiezoBolt] from ConSenses | ||
* [https://sensorise.de/solutions/smartscrew/ SmartScrew] from sensorise | |||
* [https://www.cit.fraunhofer.de/en/tech-hubs/iot-comms/q-bo.html Q-Bo] from Fraunhofer IIS | |||
Most of the existing solutions however do not fulfill the requirements of this SPP 2305. Sensors and electronics need to be fully integrated into the bolt and self-sufficient in order to maintain usability as the conventional bolt. | |||
The integration of sensors and electronics for energy delivery and processing requires sufficient design space inside the bolt. Any removal of material does however weaken the primary function. This leads to a conflict of objectives between the mechanical function (clamping force - load carrying capacity) and the sensory function (acquiring measurements with a high quality). This conflict needs to be solved by the help of models and analyses. The inevitable loss of load capacity can partly be compensated by changing the bolt's material strength class. | |||
==== Rolling bearing ==== | ==== Rolling bearing ==== | ||
Line 64: | Line 75: | ||
Physical parameters that can be measured: | Physical parameters that can be measured: | ||
* | * temperature | ||
* | * strain | ||
* | * rotational speed | ||
* | * vibration | ||
* | * lubricant condition | ||
The condition monitoring of rolling bearings is therefore a key element in the predictive maintenance of machines and systems. It enables a proactive approach | The condition monitoring of rolling bearings is therefore a key element in the predictive maintenance of machines and technical systems. It enables a proactive approach for maintenance by providing operators and engineers with important insights into the current condition of the bearings. By detecting wear, damage or other problems in good time, expensive repairs can be avoided and the service life of the machines can be extended. In an increasingly digitalized world, condition monitoring therefore plays a crucial role in ensuring the efficiency, reliability and cost-effectiveness of industrial processes. | ||
==== Gas foil bearing ==== | ==== Gas foil bearing ==== | ||
[[File:SiGFB.png|thumb|Design of the second prototype of the sensor integrating gas foil bearing (SiGFB), enabling in situ measurement of acceleration, sound, acoustic emission and temperature, dataprocessing, and BLE communication (with temporary USB for redundancy)]] | |||
Gas foil bearings (GFBs) are an advanced class of fluid dynamic bearings that utilize a thin layer of gas, typically air, as a lubricant in a gap between a rotating journal and an elastic metal foil structure, consisting typically of a supporting bump foil and a smooth top foil. This design allows for the creation of a load-bearing gas film at operational speeds, effectively minimizing friction and wear by maintaining separation between the rotor and bearing surfaces through dynamic pressure in the lubrication film. The compliant foil structure enables adaptability to varying operational conditions without the need for tight radial clearances. GFBs are thus able to function at large rotating speeds with high efficiency, low maintenance and without oil and related problems. GFBs are thus particularly suited for applications in high-speed rotating machinery where oil lubrication is undesirable or impractical, including but not limited to fuel cell blowers, air cycle machines, microturbines, and compact compressors. | Gas foil bearings (GFBs) are an advanced class of fluid dynamic bearings that utilize a thin layer of gas, typically air, as a lubricant in a gap between a rotating journal and an elastic metal foil structure, consisting typically of a supporting bump foil and a smooth top foil. This design allows for the creation of a load-bearing gas film at operational speeds, effectively minimizing friction and wear by maintaining separation between the rotor and bearing surfaces through dynamic pressure in the lubrication film. The compliant foil structure enables adaptability to varying operational conditions without the need for tight radial clearances. GFBs are thus able to function at large rotating speeds with high efficiency, low maintenance and without oil and related problems. GFBs are thus particularly suited for applications in high-speed rotating machinery where oil lubrication is undesirable or impractical, including but not limited to fuel cell blowers, air cycle machines, microturbines, and compact compressors. | ||
[[File:Sketch GFB.png|thumb|Schematic representation of bump-type gas foil bearing of generation I, top foil (1), bump foil (2), bearing sleeve (3), bearing journal (4)]] | [[File:Sketch GFB.png|thumb|Schematic representation of bump-type gas foil bearing of generation I, top foil (1), bump foil (2), bearing sleeve (3), bearing journal (4)]] | ||
Despite their advantages, GFBs can be susceptible to strong subharmonic vibrations, similar to those encountered in other hydrodynamic bearings. In addition, they may suffer from thermal instability, leading to unstable operation due to the different thermal expansion of different GFB components. The integration of sensors within GFBs for real-time monitoring of operational conditions will allow controllers to better adress these challenges. The most relevant measurement quantities in this regard include: | Despite their advantages, GFBs can be susceptible to strong subharmonic vibrations, similar to those encountered in other hydrodynamic bearings. In addition, they may suffer from thermal instability, leading to unstable operation due to the different thermal expansion of different GFB components. The integration of sensors within GFBs for real-time monitoring of operational conditions will allow controllers to better adress these challenges. The most relevant measurement quantities in this regard include: | ||
* | * vibrations | ||
* | * temperature (fields) in bearing components and gas film | ||
* | * location of the rotor | ||
Further quantities that may be deduced or measured within a GFB include: | Further quantities that may be deduced or measured within a GFB include: | ||
* | * pressure (fields) in the gas film | ||
* | * gas composition, water content | ||
* | * rotational velocity of the rotor | ||
* | * orbit of the rotor | ||
* | * current lubrication regime | ||
==== Plain bearing ==== | ==== Plain bearing ==== | ||
Besides roller bearings, plain bearings are the most frequently used machine elements in mechanical engineering, which enable the relative movements of machine parts to each other. A | Besides roller bearings, plain bearings are the most frequently used machine elements in mechanical engineering, which enable the relative movements of machine parts to each other. A plain bearing, or more commonly sliding contact bearing and slide bearing, is the simplest type of bearing, comprising just a bearing surface and no rolling elements. Therefore, the journal (i.e., the part of the shaft in contact with the bearing) slides over the bearing surface. The simplest example of a plain bearing is a shaft rotating in a hole. The effects of bearing damage are serious in economic terms as well as in terms of safety. Consequently, condition monitoring of bearings is becoming increasingly important to minimize downtime. Plain bearings are characterized by having a longer service lifetime and higher load capacity at equivalent dimensioning compared to roller bearings<ref name=":0">Lau, H. Y.; Liu, K. P.; Wong, P. L.; Wang, Wen (2012): A new design of smart journal bearing based on GMM actuators. In: ''Industrial Lubrication and Tribology'' 64 (3), S. 147–151. DOI: 10.1108/00368791211218678.</ref>. Therefore, plain bearings are especially suitable for long-term and heavy-duty applications. Accordingly, roller bearings are increasingly being replaced by plain bearings in the planetary stages of wind turbine gearboxes<ref>Ni, Sen (2022): Study on Mixed Lubrication Property of Planetary Gear Journal Bearing in Wind Turbine Gearbox. In: 2022 International Conference on Manufacturing, Industrial Automation and Electronics (ICMIAE). Rimini, Italy, 26.08.2022 - 28.08.2022: IEEE, S. 24–32.</ref>. Additionally, first concepts of main drive trains with plain bearings in wind turbines have been published<ref>Jonuschies, Ingo (2015): Hydrodynamisch wirkende zylindrische Radialgleitlager für die Rotorwellenlagerung in Windenergieanlagen. Dissertation.</ref><sup>,</sup><ref>Rolink, Amadeus; Schröder, Tim; Jacobs, Georg; Bosse, Dennis; Hölzl, Johannes; Bergmann, Philipp (2020): Feasibility study for the use of hydrodynamic plain bearings with balancing support characteristics as main bearing in wind turbines. In: ''J. Phys.: Conf. Ser.'' 1618 (5), S. 52002. DOI: 10.1088/1742-6596/1618/5/052002.</ref>. In summary, significant challenges for the safe and economical operation of a drive train can be identified: The severe effects of bearing damage in drive train systems and the current development trends leading to higher loads and increased use of plain bearings in drive trains. | ||
Regarding the type and direction of the forces occurring between the moving machine elements, a distinction is drawn between statically or dynamically loaded radial and axial plain bearings<ref>Sauer, Bernd (2018): Konstruktionselemente des Maschinenbaus 2. Berlin, Heidelberg: Springer Berlin Heidelberg.</ref>. Furthermore, a distinction between plain bearings without the use of an intermediate medium, which are permanently subject to wear, and those with a separating medium (typically oil) can be made. Plain bearings using a separating medium are advantageous in terms of their friction behavior, which can be optimized to the extent of no wear occurring during operation | Regarding the type and direction of the forces occurring between the moving machine elements, a distinction is drawn between statically or dynamically loaded radial and axial plain bearings<ref>Sauer, Bernd (2018): Konstruktionselemente des Maschinenbaus 2. Berlin, Heidelberg: Springer Berlin Heidelberg.</ref>. Furthermore, a distinction between plain bearings without the use of an intermediate medium, which are permanently subject to wear, and those with a separating medium (typically oil) can be made. Plain bearings using a separating medium are advantageous in terms of their friction behavior, which can be optimized to the extent of no wear occurring during operation. However, the wear-free state can only be ensured if solid contact between the two contact partners, the bearing bush and the shaft, is completely avoided. Plain bearings, which are operated using a separating medium and therefore can enable wear-free operation, are classified into hydrostatic and hydrodynamic plain bearings<ref>Hinzen, Hubert (2022): Hubert Hinzen: Maschinenelemente/Lager, Welle-Nabe-Verbindungen, Getriebe. 5., aktualisierte Auflage. Berlin: De Gruyter Oldenbourg (De Gruyter Studium, 2).</ref>. In case of hydrostatic plain bearings, the wear-free state is achieved by applying pressure to the lubricating film externally by a pump. Therefore, the state of motion created, does not influence the separation of the surfaces relative to each other. In the case of hydrostatic plain bearings, the lubrication gap height can be controlled by using active hydraulic chamber systems <ref>Althaus, Josef (1991): Eine aktive hydraulische Lagerung für Rotorsysteme (Fortschritt-Berichte VDI, Series 11, N154).</ref><sup>,</sup><ref>Kurth, R.; Tehel, R.; Päßler, T.; Putz, M.; Wehmeyer, K.; Kraft, C.; Schwarze, H. (2019): Forming 4.0: Smart machine components applied as a hybrid plain bearing and a tool clamping system. In: ''Procedia Manufacturing'' 27, S. 65–71. DOI: 10.1016/j.promfg.2018.12.045.</ref><sup>,</sup><ref>Santos, Ilmar F. (2011): Trends in Controllable Oil Film Bearings. In: K. Gupta (Hg.): IUTAM Symposium on Emerging Trends in Rotor Dynamics, Bd. 1011. Dordrecht: Springer Netherlands (IUTAM Bookseries), S. 185–199.</ref>. Due to active separation of the wear surfaces, sensor-integrated condition monitoring is of secondary relevance for hydrostatic plain bearings. The friction and wear behavior of the surfaces moving relative to each other in hydrodynamic plain bearing is decisively dependent on their relative speed. Wear-free conditions are only achieved at sufficient relative speed. Hydrodynamic axial plain bearings, which primarily support axial forces in the direction of the shaft, are used less frequently compared to radial hydrodynamic plain bearings. Accordingly, the following section will focus primarily on hydrodynamic radial plain bearings and the possibilities for condition monitoring. | ||
For monitoring hydrodynamic radial plain bearings, the measurement of a number of quantities is well established. Possibly used monitoring principles are: | For monitoring hydrodynamic radial plain bearings, the measurement of a number of quantities is well established. Possibly used monitoring principles are: | ||
* | * temperature monitoring | ||
* | * acoustic emission | ||
* | * lubricant monitoring | ||
* | * friction torque | ||
* | * orbital analysis | ||
* | * electric contact resistance | ||
* | * acceleration monitoring | ||
==== Shaft coupling ==== | ==== Shaft coupling ==== | ||
Couplings are mechanical elements that connect two shafts in order to transmit mechanical power from one to the other. Furthermore, they i) can compensate for shaft misalignment, ii) have a switching function to interrupt or limit the power flow, and iii) compensate for shocks. The industry provides a variety of application-specific designs, which satisfy diverse requirement profiles. VDI 2240 provides a suitable basis for selecting and classifying couplings according to their requirements. A subdivision is made according to switchable (clutch) and non-switchable (couplings) couplings. Based on this classification, different possible measurement quantities result. For couplings, the measured variables of a torque and rotational speed are particularly relevant. Furthermore, temperature, wear, shaft misalignments, restoring and reaction forces, and vibrations can be significant. For clutches, which also includes brakes, the measurement of the same parameters is desirable. Additionally, relevant parameters are clutch engagement and slip between the two hubs. <ref name="Kirchner2024" /> | |||
[[File:Types of sensor-integrating couplings.png|thumb|Sensor-integrating | [[File:Types of sensor-integrating couplings.png|thumb|Sensor-integrating gearbox, focusing on sensor-integrating couplings and their measuring task, exemplified by a sleeve coupling (1), a bellow coupling (2), and an elastic jaw coupling (3).]] | ||
Important features that are of interest for these machine elements are: | Important features that are of interest for these machine elements are: | ||
* | * torque, | ||
* | * rotational speed, | ||
* | * temperature, | ||
* | * shaft misalignment and | ||
* | * vibration | ||
An important subclass of couplings are elastic couplings such as jaw couplings. They can be used to compensate for shaft misalignments and can mitigate critical torque shocks. Couplings are | An important subclass of couplings are elastic couplings such as jaw couplings. They can be used to compensate for shaft misalignments and can mitigate critical torque shocks. Couplings are ideal components for measuring process data as they are located directly in the power flow. | ||
==== Splined shaft ==== | ==== Splined shaft ==== | ||
Splined shafts are a shaft-hub connection | Splined shafts are a shaft-hub connection that are used to transmit torque. Splined shafts are standardized machine elements according to DIN 5480 and ISO 4156. As splined shafts are located directly in load path of machines, they are suitable as a sensor-integrated machine element for making statements about the operating status of the machine and the experienced loads. The main type of load is torsion, but other load cases with additional bending moment or shear force can occur. | ||
The physical quantities relevant for the primary function are: | The physical quantities relevant for the primary function are: | ||
* | * torque | ||
* | * bending torque | ||
* | * fit of the teeth | ||
The physical quantities are beneficial to | The physical quantities are beneficial to measure: | ||
* | * torque | ||
* | * rotational speed | ||
* | * temperature | ||
==== Feather key ==== | ==== Feather key ==== | ||
Seltmann et al. <ref name="Kirchner2024" />developed a feather key (FK) for measuring the circumferential force by means of topology optimization, where the main dimensions are based on DIN 6885. The main idea is as follows: The FK is normally subjected to a non-uniform surface pressure, which, in addition to the torque, also depends on the hub geometry, resulting in a complex deformation of the FK. In order to determine the resulting circumferential force from this deformation field, the deformation of the FK must be measured with a large number of strain gauges. This is followed by complex calculations to determine the resulting circumferential force. With the aid of topology optimization, however, the geometry of the FK is adapted so that it always deforms approximately according to a linear combination of a few deformation modes under different non-uniform surface pressures. This reduces the number of strain gauges required to the number of deformation modes and simplifies the calculation of the resulting force. The boundary conditions were simplified for the topology optimization. For testing under practical boundary conditions, the geometry of the stiffness conditioned FK was simplified and a finite element model was created, as shown [[Index.php?title=Media:Feather key.png|here]]. For showing differences in pressure distribution dependent on the hub geometry two different cases are simulated. A torque is applied, and the deformation of the FK in the numerical model is studied. It is shown that the deformation can be described by a linear combination of two deformation modes, so the deformation of the FK should be measurable by applying two strain gauges. | |||
[[File:Feather key.png|thumb|268x268px|a) Interpreted stiffness conditioned feather key. b) Entire assembly for the finite element model.]] | [[File:Feather key.png|thumb|268x268px|a) Interpreted stiffness conditioned feather key. b) Entire assembly for the finite element model.]] | ||
The most relevant physical quantities are: | The most relevant physical quantities are: | ||
* | * torque | ||
* | * shear stress | ||
* | * bearing stress | ||
* | * material properties | ||
* | * key dimensions (width, height, length) | ||
==== Seal ==== | ==== Seal ==== | ||
'' | Seals are widespread machine elements for separating adjacent areas between which an exchange of substances is to be suppressed to a desired extent. In addition to the seal itself, a sealing system therefore also includes the interacting counter surface as well as the media applied. | ||
In the case of a rotary shaft seal used at shaft exits from machine housings, shaft rotation causes a relative motion between sealing lip and counter surface. As a consequence, an active sealing mechanism evolves in the sealing contact, enabling the lubricant to be pumped towards the oil sump. Within this context, the proper sealing function depends on the interaction of various ambient and operational parameters, whose knowledge enables conclusions about the condition of the sealing system. [[File:Sensor-integrating gear box, focusing on sensor-integrating radial shaft seal.png|thumb|Sensor-integrating gear box, focusing on sensor-integrating radial shaft seal]]Since there are no reliable methods for prediction of a rotary shaft seal’s service life<ref name="Kirchner2024" />, Thielen et al. proposed sensor integration approaches aiming for in-situ measurement of several parameters, particularly those related to the sealing mechanism<ref>Thielen, S., Stiemcke, Y., Sauer, B., Koch, O., Sivasothy, P., Seewig, J., Rheinländer, C., & Wehn, N. (2022). Sensorintegrierendes Maschinenelement Radialwellendichtring zur Überwachung von Betriebszustand und Schmierstoffqualität, ''Dresdner Maschinenelemente Kolloquium 2022'', S.127-139</ref>. These include: | |||
* oil sump temperature | |||
* oil sump pressure | |||
* lubricant quality | |||
* sealing contact temperature<ref>Stiemcke, Y., Thielen, S., Sauer, B., Koch, O., Uebel, J., Seewig, J., Rheinländer, C., Wehn, N., & Nikolaus, K.(2024). Entwicklung eines Sensorintegrationsverfahrens zur in situ Erfassung der Kontakttemperatur von Radialwellendichtringen, ''Dresdner Maschinenelemente Kolloquium 2024''</ref> | |||
* sealing contact friction (friction torque)<ref name=":2">Stiemcke, Y., Thielen, S., & Koch, O. (2024). Theoretical concept for in-situ condition monitoring of rotary shaft seals using surface strain-based analysis of the deformation state. ''Engineering Research-Forschung im Ingenieurwesen'' (Preprint). URN: urn:nbn:de:hbz:386-kluedo-81078.</ref> | |||
* sealing lip preload<ref name=":2" /> | |||
The sensor system's power supply as well as data transmission are realised wirelessly so that the rotary shaft seal can also be retrofitted to existing machines. | |||
== Interaction of sensor system and machine element == | == Interaction of sensor system and machine element == | ||
=== Calculation methodology for service life / load carrying capacity === | === Calculation methodology for service life / load carrying capacity === | ||
==== Gears ==== | |||
Involute gears have a standardized set of defining parameters which may be found in ISO 21771. The gear geometry of the vast majority of gears made from steel for small, medium and large applications is defined according to that standard. Load carrying capacity for these gears is analyzed by the methodology defined in ISO 6336. Gear failures may be distinguished in pitting, tooth root breakage, micro-pitting, scuffing, tooth flank breakage and wear. The methodology for each failure mode is briefly characterized in the following: | |||
Pitting damage is a local material breakout of the active tooth flank. As a characteristic value the tooth contact pressure is calculated and the safety factor or fatigue life may be derived. The S-N-curve for the gear needs to be defined, e.g. in relation to the material and heat treatment applied. | |||
Tooth root breakage is a breakout of one or more teeth starting in the tooth root fillet. As a characteristic value the tooth root stress is calculated and the safety factor or fatigue life may be derived. The S-N-curve for the gear needs to be defined, e.g. in relation to the material and heat treatment applied. | |||
Micro pitting is a continuing breakout of very small particles out of the active tooth flank . As a characteristic value the relative lubricating film thickness in tooth contact is used and a safety factor or a lifetime may be derived. The limit is not defined by an S-N-curve but by a reference value of required minimal lubricating film thickness. | |||
Scuffing is a local welding of the meshing tooth flanks and a consecutive separation. As a characteristic value the contact temperature in tooth contact is used and a safety factor may be derived. Scuffing is characterized as an instantaneous damage and therefore not decribed by an S-N-curve. | |||
Tooth flank breakage starts as a crack of the tooth flank beneath the surface and a successive crack propagation through the whole tooth until breakout of the upper part of the tooth. Characteristic value is the equivalent stress in the tooth in comparison to the stress limit. | |||
A documentation of the path of calculation may be found in ISO 6336 and is not given in detail here. | |||
==== Bolts ==== | |||
[[File:Method procedure.png|alt=Procedure for design space optimization for sensor integration into bolts|thumb|Procedure for design space optimization for sensor integration into bolts, according to [https://publikationen.bibliothek.kit.edu/1000169793 Peters et al.]]] | |||
Bolts are standardized in geometry according to ISO 4014 and dimensioned according to VDI 2230. An objective for the sensor integration is to maintain the load carrying capacity as much as possible while providing a sufficient measurement quality. This usually leasds to a conflict of objectives in many machine elements, because the sensory function needs space inside the machine element, that is also needed for providing the mechanical function. Especially for bolts this is a problem, because the design space is rather small. | |||
For bolts, an optimization function is necessary that optimizes the design space while taking the mechanical and sensory function into consideration. The mechanical function can be evaluated by the change in v. Mises stress, the sensory function needs to be modelled according to the sensors used. | |||
==== Feather keys ==== | |||
[[File:FeatherKeyTest.jpg|thumb|Quasi-static test to identify plastic deformation of the feather key which occurs as failure criterion]] | |||
The fatigue strength of a feather key connection can be calculated by different concepts. On the one hand, the fatigue strength of the notched shaft can be carried out by the German national standard DIN 743 and on the other hand, the transmittable torque can be calculated by the German national standard DIN 6892, which addresses the pressure distribution between the feather key and the shaft notch and the pressure distribution between the feather key and the hub notch. This standard is divided in three methods, of which method C is relevant in the context of sensor-integrating feather key connections. In the elastic deformation range, there is a linear relationship between torque and angle of twist. When the key is plastically deformed, the relationship between torque and angle becomes non-linear, as shown by the evaluation of a quasi-static test in the [[:File:FeatherKeyTest.jpg|right-hand side figure]]. | |||
The | Since the concept of calculating circumferential forces is based on the theory of linear elasticity, the sensor-integrating feather key must not show any plastic deformation. The corresponding threshold value for the transmittable torque can be estimated using method C of DIN 6892, where a critical pressure <math display="inline">p_{\rm{crit}}</math>, the height of the feather key <math display="inline">h</math> and the supporting height in the “critical” notch <math>t_{1,\rm{sup}}</math>, the supporting length <math display="inline">l_{\rm{sup}}</math>, the number of feather keys <math display="inline">i</math>, the supporting factor <math display="inline">\varphi</math> and the shaft diameter <math display="inline">d</math> are taken into account. The transmittable torque is given by | ||
= | <math>M_{\rm{trans}}=p_{\rm{crit}} \cdot (h-t_{1,\rm{sup}}) \cdot l_{\rm{sup}}\cdot \frac{d}{2} \cdot i \cdot \varphi</math>. | ||
=== Mechanical integration === | === Mechanical integration === | ||
==== Prototypes ==== | ==== Prototypes ==== | ||
In order to test the developed concept it is important to start with the production of prototpyes as early as possible to gain a better understanding and to mitigate or even detect the amount of possible failure modes. In this way, possible errors that were not previously thought of can be identified. | In order to test the developed concept it is important to start with the production of prototpyes as early as possible to gain a better understanding and to mitigate or even detect the amount of possible failure modes. In this way, possible errors that were not previously thought of can be identified. Hence prototypes serve as testing objects to gather knowledge about the function behaviour structure connection. | ||
==== Wiring / connectors ==== | ==== Wiring / connectors ==== | ||
When cables are used inside a machine element they are subjected to´(i) cyclic strains or (ii) very high strains and stresses. It follows that they often break down. In order to eleviate this problem, micro coaxial cables can be used. | When cables are used inside a machine element they are subjected to´(i) cyclic strains or (ii) very high strains and stresses. It follows that they often break down. In order to eleviate this problem, micro coaxial cables can be used. | ||
=== Testing / validation === | === Testing / validation === | ||
Continuous testing of new components is essential during the development of SiME. This reduces the risk of errors accumulating. Ideally, the individual components are tested separetly at the beginning. This speeds up the process and errors can be detected accuratly and early. | Continuous testing of new components is essential during the development of SiME. This reduces the risk of errors accumulating. Ideally, the individual components are tested separetly at the beginning. This speeds up the process and errors can be detected accuratly and early. | ||
Testing includes the question how the SiME performs under developing damages. This poses several challenges: Not only have the sensors to be robust enough to resist often harsh conditions for damaging the machine elements. Also several SiMe have to be available for testing and potential destruction by the test. Furthermore an adequate test rig to apply realistic operating conditions to the specimens has to be available. All this leads to the fact that the first tests of the campaign are mostly measurement tests and only later in the project test conditions will become more challenging and related to real operation of the SiME. | |||
== Operating strategy == | == Operating strategy == | ||
=== Data handling === | === Data handling === | ||
The amount of data generated by SiME depends on the employed sensor principle and the data acquisition frequency. The strategy for the handling of this data will also have to be informed by other boundary conditions, such as the limitation of the communication system and the energy required to store, process and transfer the data. Important concepts for dealing with the data are algorithmic reduction and buffering. The former reduces the amount of data that has to be handled through processing. The latter deals with concepts for the temporary storage of data before further steps can be taken. | |||
==== Algorithms for reduction ==== | ==== Algorithms for reduction ==== | ||
Data processing methods: one of the most efficient ways to compress data may be to calculate the target values directly from them, reducing the data to only the relevant information of interest. | Data processing methods: one of the most efficient ways to compress data may be to calculate the target values directly from them, reducing the data to only the relevant information of interest. | ||
Since many fault detection approaches still rely on external high-performance measurement systems unsuitable for in-situ integration, algorithms for damage detection have to be adapted for low-power embedded systems, such as Microcontrollers (MCUs). Moreover, the minimum required data sample rate necessary for damage detection needs to be determined in order to | Since many fault detection approaches still rely on external high-performance measurement systems unsuitable for in-situ integration, algorithms for damage detection have to be adapted for low-power embedded systems, such as Microcontrollers (MCUs). Moreover, the minimum required data sample rate necessary for damage detection needs to be determined in order to acquire data in the most efficient way, which can be, for example, achieved by using a downsampling approach. One typical use case for data reduction is gear condition monitoring, which can prevent unexpected downtimes or sudden failure of machinery <ref name="Rupprecht2023" />. | ||
==== Methods for buffering ==== | ==== Methods for buffering ==== | ||
Ringbuffer / FiFo: A type of buffer, where a new element is always written over the oldest element in the buffer. | Ringbuffer / FiFo: A type of buffer, where a new element is always written over the oldest element in the buffer. That means its purpose is to always preserve the most recent data written. | ||
When implementing any of these techniques, the choice of memory location is crucial: in RAM the data is more easily accessible and consumes less power for writing / reading, but the memory is volatile and the data will be lost on | When implementing any of these techniques, the choice of memory location is crucial: in RAM the data is more easily accessible and consumes less power for writing / reading, but the memory is volatile and the data will be lost on power loss. This type of buffer can also be directly implemented in digital sensors, allowing the host processor to retrieve batches of data at longer intervals. In non-volatile memory like Flash / EEPROM the data will persist in case of power loss, also larger storage sizes are available, but the reading and writing consumes more power. | ||
==== Outlook on the use of data ==== | ==== Outlook on the use of data ==== | ||
The ultimate goal for most sensor-integrated machine element applications is condition monitoring of the element itself, nearby components or a machine assembly as a whole. This has to be taken into account when designing a data handling strategy. | |||
However, in research applications it is often necessary to first collect more extensive preliminary data to learn about the underlying degradation process. Only after the data generating process is understood a fitting data handling strategy can be designed that will efficiently handle the information while preserving the characteristic patterns for later examination. | |||
=== Operating strategy for processors === | === Operating strategy for processors === | ||
Line 207: | Line 240: | ||
==== Duty Cycle ==== | ==== Duty Cycle ==== | ||
The processor operates on a schedule and reverts to a low-power mode | The processor operates on a schedule and reverts to a low-power mode in between the active phases. This can be realized using timer interrupts. In some modes, peripherals may be active while the processors are not, collecting or preparing data for the active phase. | ||
==== Eventbased ==== | ==== Eventbased ==== | ||
The processor operates after an event has happened. This can be | The processor operates after an event has happened. This can be realisrealizeded using interrupt signals from either internal hardware like comparators or external hardware, like additional sensors. | ||
=== Data transfer === | === Data transfer === | ||
Line 225: | Line 249: | ||
Since electromagnetic waves are shielded and reflected to some extent by metal, the integration of sensors in metallic machine elements poses a challenge for communication. However, contrary to common perception, it is possible to send data out of a fully enclosed metal case. Real metal has finite resistance, and the magnetic field component can penetrate a faraday cage, leading to strong damping (about >50dB). | Since electromagnetic waves are shielded and reflected to some extent by metal, the integration of sensors in metallic machine elements poses a challenge for communication. However, contrary to common perception, it is possible to send data out of a fully enclosed metal case. Real metal has finite resistance, and the magnetic field component can penetrate a faraday cage, leading to strong damping (about >50dB). | ||
An alternative approach to transmit data in or out of | An alternative approach to transmit data in or out of a metallic machine to communicate with the SiME can be achieved by using ultra sonic waves. Those waves can penetrate through metal with little dampening. This approach is used in a variety of applications ['''cite'''] and can be adapted for the use in machine elements. | ||
==== Protocols ==== | ==== Protocols ==== | ||
Long Range Wide Area Network (LoRaWAN) is a low-power wireless network protocol operating at the network layer. It is defined by the LoRa Alliance and provides specifications that are freely available. Additionally, software building blocks are accessible as open-source software. | Long Range Wide Area Network (LoRaWAN) is a low-power wireless network protocol operating at the network layer. It is defined by the LoRa Alliance and provides specifications that are freely available. Additionally, software building blocks are accessible as open-source software. | ||
Line 237: | Line 257: | ||
LoRa end devices and gateways in LoRaWAN utilize a proprietary and patented transmission method based on a chirp spread spectrum modulation technique called “LoRa". LoRa operates at the physical layer and is asymmetrically designed for energy efficiency, achieving uplink communication ranges of over 10 km. Data rates range from 292 bit/s to 50 kbit/s. Various operational modes, including quasi-continuous downlink communication, are possible, although the latter affects energy efficiency. The LoRa Alliance also refers to this technology as Low Power Wide Area Networks (LPWANs). LoRa uses different regional frequency bands in the ISM and SRD bands. For example, in Europe, the frequency band ranges from 433.05 to 434.79 MHz (ISM Band Region 1) and from 863 to 870 MHz (SRD Band Europe). The coverage extends from 2 km in urban areas to 40 km in rural regions. Notably, LoRa’s penetration capabilities allow it to reach even basement areas <ref>https://www.lora-wan.de/</ref>. | LoRa end devices and gateways in LoRaWAN utilize a proprietary and patented transmission method based on a chirp spread spectrum modulation technique called “LoRa". LoRa operates at the physical layer and is asymmetrically designed for energy efficiency, achieving uplink communication ranges of over 10 km. Data rates range from 292 bit/s to 50 kbit/s. Various operational modes, including quasi-continuous downlink communication, are possible, although the latter affects energy efficiency. The LoRa Alliance also refers to this technology as Low Power Wide Area Networks (LPWANs). LoRa uses different regional frequency bands in the ISM and SRD bands. For example, in Europe, the frequency band ranges from 433.05 to 434.79 MHz (ISM Band Region 1) and from 863 to 870 MHz (SRD Band Europe). The coverage extends from 2 km in urban areas to 40 km in rural regions. Notably, LoRa’s penetration capabilities allow it to reach even basement areas <ref>https://www.lora-wan.de/</ref>. | ||
Other protocols that can be used in the context of SiME are: | |||
* Bluetooth Low Energy | |||
* Zigbee | |||
* Mioty | * Mioty | ||
* Sigfox | * Sigfox | ||
* NB-IOT | * NB-IOT | ||
=== Validation strategy === | |||
A crucial step for the evaluation of an operating strategy is the assessment of algorithm execution time, especially when using low-power embedded microcontrollers. If the execution time of selected algorithms cannot meet the timing requirements of a specific use-case considering them in the operating strategy is not feasible. Thus, it is important to consider algorithm execution time right from the beginning of the system design. Thereby, performance benchmarking methods provide tools to effectively measure and predict algorithm execution time within the design process <ref name="Rupprecht2022" />. For early design states, early-stage execution time prediction approaches, for example, based on sparse measurements can give a first estimate about algorithm execution times on different hardware devices by simultaneously minimizing measurement effort <ref name="Rupprecht2024" />. Challenges in measuring software execution time on heterogeneous devices can be mitigated by a systematic selection of execution time measurement methods within the benchmarking setup <ref name="Rupprecht2023b" />. | |||
== Microsystem technology == | == Microsystem technology == | ||
=== Sensor systems === | === Sensor systems === | ||
Intelligent sensor systems, that are used to measure a variety of different measurands, are relevant examples for microsystems in the context of | Intelligent sensor systems, that are used to measure a variety of different measurands, are relevant examples for microsystems in the context of SiME. In these sensor systems, signal processing is moving ever closer to the point of measurement, resulting in decentralized, independent systems<ref name="Mescheder2004" />. Sensor systems in the context of microsystem technology are characterized by different aspects:<ref name="Völklein2006" /> | ||
* | * small size, mass and minimal energy consumption of the system, | ||
* | * high reproducibility of the system parameters in production, | ||
* | * compensation of environmental influences and cross sensitivity through localization of sensors and signal processing in the smallest possible space, | ||
* | * material and cost savings through parallel production of large quantities and | ||
* | * high reliability through integration, reduction of interferences by reducing electrical contacts and cables. | ||
==== Overview of measuring principles ==== | ==== Overview of measuring principles ==== | ||
The ''measuring principle'' is defined according to the Joint Committee for Guides in Metrology (JCGM) and the German Institute for Standardization (dt.: Deutsches Institut für Normung (DIN)) as phenomenon (physical, chemical or biological) serving as a basis of a measurement. The measuring principle allows another variable to be measured instead of the measurand to determine the value of the measurand from its value. It is based on a physical, chemical or biological phenomenon or effect that can always be reproduced with a known law between the measurand and the measurand variable. In the following, different measuring principles for measurands relevant in the context of | The ''measuring principle'' is defined according to the Joint Committee for Guides in Metrology (JCGM) and the German Institute for Standardization (dt.: Deutsches Institut für Normung (DIN)) as phenomenon (physical, chemical or biological) serving as a basis of a measurement. The measuring principle allows another variable to be measured instead of the measurand to determine the value of the measurand from its value. It is based on a physical, chemical or biological phenomenon or effect that can always be reproduced with a known law between the measurand and the measurand variable. In the following, different measuring principles for measurands relevant in the context of SiME are outlined, whereby the focus is on physical phenomenons.<ref name="Brinkmann2012" /><ref name="DIN1319-1" /> | ||
===== Temperature ===== | ===== Temperature ===== | ||
Temperature can be measured using three different principles: | Temperature can be measured using three different principles: | ||
# | # silicon Bandgap: this type of sensor depends on the temperature dependence of the forward voltages of diodes. It is used in most temperature sensors in integrated curcuits, since it can be easily integrated into silicon wafers. Sensor-Examples: TI TMP119 (0.08°C accuracy, 5 µA at 1.7 - 5.5 V) | ||
# | # seebeck / thermoelectric effect: The voltage is produced between different metals if they are contacted at different temperatures. These combinations are called thermocouples. | ||
# | # resistance: the electric resistance of resistors changes with temperature. Therefore, the resistance of certain materials like platinum can be used as temperature sensor. Todo so a resistor made out of platinum with the addition of other elements for long-term stability can be used. | ||
===== Strain ===== | ===== Strain ===== | ||
Strain can be measured using several approaches: | Strain can be measured using several approaches: | ||
# | # strain gauges | ||
# | # piezo elements | ||
# | # dielectric elastomer sensors (DES) | ||
With known material properties, the acting load can be derived from the measured strain. However, most approaches to strain measurement have different sensitivities depending on the direction of the strain. It is advantageous to use a deformation body that decouples the acting components to different strain ranges, if more than one force component is to be measured. Ideally, a sensor designed to measure three forces would have three distinct zones where the strains respond proportionally to only one force component each. In some cases, the use of Wheatstone bridge circuits can help to reduce cross-sensitivity<ref>https://en.wikipedia.org/wiki/Wheatstone_bridge</ref><ref>F. Herbst ''et al''., "Multi-axis Force Sensor for Sensor-integrating Bolts," ''2022 IEEE Sensors'', Dallas, TX, USA, 2022, pp. 1-4, doi: 10.1109/SENSORS52175.2022.9967220 </ref>. | |||
===== Vibration ===== | ===== Vibration ===== | ||
Vibrations, acceleration, respectively, can be measured using several measuring principles: | Vibrations, acceleration, respectively, can be measured using several measuring principles: | ||
# | # capacitive (MEMS) | ||
# | # piezo-electric | ||
==== Electromagnetic sensors ==== | ==== Electromagnetic sensors ==== | ||
Electromagnetic testing methods include a wide variety of testing techniques. Typical methods are the impedance method, conventional eddy current testing and magnetic inductive testing. At least one coil is required for electromagnetic testing. In addition to the exciter coil, a measuring coil and a compensation coil can be added. If the electrical conductivity and/or the magnetic permeability of the test object changes, this can be detected non-destructively on the basis of the signal change <ref>Stroppe, H., & Schiebold, K. (2011). ''Wirbelstrom-Materialprüfung: ein Lehr-und Arbeitsbuch für Ausbildung und Prüfpraxis; mit 29 Tabellen''. Castell-Verlag.</ref>. For instance, in combination with an austenitic metastable stainless steel, overloading of the component can be detected. The measuring effect is the transformation of paramagnetic austenite into ferromagnetic martensite when a certain load is exceeded <ref>Gansel, R., Quanz, M., Lohrengel, A., Maier, H. J., & Barton, S. (2024). Qualification of Austenitic Stainless Steels for the Development of Load-Sensitive Material Sensors. ''Journal of Materials Engineering and Performance'', 1-13.</ref>. | Electromagnetic testing methods include a wide variety of testing techniques. Typical methods are the impedance method, conventional eddy current testing and magnetic inductive testing. At least one coil is required for electromagnetic testing. In addition to the exciter coil, a measuring coil and a compensation coil can be added. If the electrical conductivity and/or the magnetic permeability of the test object changes, this can be detected non-destructively on the basis of the signal change <ref>Stroppe, H., & Schiebold, K. (2011). ''Wirbelstrom-Materialprüfung: ein Lehr-und Arbeitsbuch für Ausbildung und Prüfpraxis; mit 29 Tabellen''. Castell-Verlag.</ref>. For instance, in combination with an austenitic metastable stainless steel, overloading of the component can be detected. The measuring effect is the transformation of paramagnetic austenite into ferromagnetic martensite when a certain load is exceeded <ref>Gansel, R., Quanz, M., Lohrengel, A., Maier, H. J., & Barton, S. (2024). Qualification of Austenitic Stainless Steels for the Development of Load-Sensitive Material Sensors. ''Journal of Materials Engineering and Performance'', 1-13.</ref>. | ||
One way of measuring large strains is to use dielectric elastomer sensors (DES) <ref>Rosset, S., & Shea, H. R. (2016). Small, fast, and tough: Shrinking down integrated elastomer transducers. ''Applied Physics Reviews'', ''3''(3)</ref>. They consist out of a dielectric layer which is sandwiched between two compliant electrodes. An electric field will form if an electric potential difference is applied on the two electrodes and a capacitance can be measured. Electrically, DES behave like plate capacitors. A deformation of the DES leads to a change in the capacitance which can then be used to measure the '''strain''' or '''force''' that caused this deformation. | One way of measuring large strains is to use dielectric elastomer sensors (DES) <ref>Rosset, S., & Shea, H. R. (2016). Small, fast, and tough: Shrinking down integrated elastomer transducers. ''Applied Physics Reviews'', ''3''(3)</ref>. They consist out of a dielectric layer which is sandwiched between two compliant electrodes. An electric field will form if an electric potential difference is applied on the two electrodes and a capacitance can be measured. Electrically, DES behave like plate capacitors. A deformation of the DES leads to a change in the capacitance which can then be used to measure the '''strain''' or '''force''' that caused this deformation. | ||
==== Robustness and Resilience ==== | ==== Robustness and Resilience ==== | ||
The robustness and resilience of the sensor system are crucial for its proper function, even in the presence of disturbances, as well as the reliability of the measuring data provided by a | The robustness and resilience of the sensor system are crucial for its proper function, even in the presence of disturbances, as well as the reliability of the measuring data provided by a SiME. Therefore, disturbances that may occur in the later use context of the SiME must be identified and considered early on in its development. | ||
On the one hand, robustness and resilience must be taken into account when selecting components and modules for the sensor system, e.g., sensors. Sensors can rely on different measuring principles, physical effects, respectively, that change the measurand into an electric measuring signal. These effects may be more or less susceptible to disturbances occurring in the later use context of the system. Hence, it is reasonable to select components that are less susceptical to disturbances occurring in the later use context of the | On the one hand, robustness and resilience must be taken into account when selecting components and modules for the sensor system, e.g., sensors. Sensors can rely on different measuring principles, physical effects, respectively, that change the measurand into an electric measuring signal. These effects may be more or less susceptible to disturbances occurring in the later use context of the system. Hence, it is reasonable to select components that are less susceptical to disturbances occurring in the later use context of the SiME. Since not all manufacturers provide the information required to conduct this selection, experimental benchmark and functional tests are a suitable approach for obtaining this information. | ||
On the other hand, robustness and resilience must also be taken into account when the sensor system is verified or tested. In this context, early verifications and testings of the individual components and modules of the sensor system in the later environment, e.g. in oil, was found to be a promising approach by many projects. In order to protect the sensor system and susceptible modules from disturbances, different approaches can be chosen, e.g. an encapsulation or shielding of the components or modules. Mathias et al.<ref name="Mathias2010" /> cluster these different approaches based on their point of attack in the cause-and-effect chain into three so-called Robust Design strategies: elimination of disturbance, elimination of disturbance influence and elimination of disturbance impact. | On the other hand, robustness and resilience must also be taken into account when the sensor system is verified or tested. In this context, early verifications and testings of the individual components and modules of the sensor system in the later environment, e.g. in oil, was found to be a promising approach by many projects. In order to protect the sensor system and susceptible modules from disturbances, different approaches can be chosen, e.g. an encapsulation or shielding of the components or modules. Mathias et al.<ref name="Mathias2010" /> cluster these different approaches based on their point of attack in the cause-and-effect chain into three so-called Robust Design strategies: elimination of disturbance, elimination of disturbance influence and elimination of disturbance impact. | ||
Line 293: | Line 319: | ||
===== Piezoelectric energy harvesting ===== | ===== Piezoelectric energy harvesting ===== | ||
Piezoelectric energy harvesters comprise a piezoelectric element, its mechanic fixation and electronics. When the piezoelectric element experiences mechanical stress it produces a charge. This charge is then rectified and converted to the needed voltage by the electronics. Piezoelectric harvesters are not available as premade products but have to be constructed custom for each application, since their construction depends on the amplitude, direction and frequency of the stress. The core is formed by a premade piezoelectric element that is sensitive to stress in the right direction and at the right frequencies, the mechanical fixation is then built around it to maximize the stress and amplitude. | Piezoelectric energy harvesters comprise a piezoelectric element, its mechanic fixation and electronics. When the piezoelectric element experiences mechanical stress it produces a charge. This charge is then rectified and converted to the needed voltage by the electronics. Piezoelectric harvesters are not available as premade products but have to be constructed custom for each application, since their construction depends on the amplitude, direction and frequency of the stress. The core is formed by a premade piezoelectric element that is sensitive to stress in the right direction and at the right frequencies, the mechanical fixation is then built around it to maximize the stress and amplitude. | ||
===== Thermoelectric energy harvesting ===== | ===== Thermoelectric energy harvesting ===== | ||
Thermoelectric energy harvesting is a method for capturing energy in processes by utilizing temperature differences and converting them to electrical energy<ref>Kishore, R. A., & Priya, S. (2018). A Review on Low-Grade Thermal Energy Harvesting: Materials, Methods and Devices. Materials (Basel, Switzerland), 11(8).</ref>. Thermogenerators (TEG) are devices that utilize occurring temperature differences and convert those temperature gradients into electricity based on the thermoelectrical effects<ref>Snyder, G. J., & Toberer, E. S. (2008). Complex thermoelectric materials. Nature materials, 7(2), 105–114.</ref>. Thermoelectric harvesting is an emerging technology, which is increasingly explored and further developed regarding its efficiency and reliability<ref>Abdal-Kadhim, A. M., & Leong, K. S. (42017). Application of thermal energy harvesting from low-level heat sources in powering up WSN node. In 2017 2nd International Conference on Frontiers of Sensors Technologies (ICFST) (pp. 131–135). IEEE.</ref><ref>Attivissimo, F., Lanzolla, A. M. L., Passaghe, D., Paul, M., Gregory, D., & Knox, A. (52014). Photovoltaic-thermoelectric modules: A feasibility study. In 2014 IEEE International Instrumentation and Measurement Technology Conference (I2MTC) Proceedings (pp. 659–664). IEEE.</ref><ref>Bhattacharya, M., Ranjan, M., Kumar, N., & Maiti, T. (2021). Performance Analysis and Optimization of a SnSe-Based Thermoelectric Generator. ACS Applied Energy Materials, 4(8), 8211–8219.</ref>. This also includes the low-level heat range, in which the TEGs are able to harvest energy at occurring temperature differences of a few Kelvin<ref>Gou, X., Xiao, H., & Yang, S. (2010). Modeling, experimental study and optimization on low-temperature waste heat thermoelectric generator system. Applied Energy, 87(10), 3131–3136.</ref><ref>Niu, X., Yu, J., & Wang, S. (2009). Experimental study on low-temperature waste heat thermoelectric generator. Journal of Power Sources, 188(2), 621–626.</ref>. | |||
===== Electromagnetic energy harvesting ===== | ===== Electromagnetic energy harvesting ===== | ||
Electromagnetic energy harvesting is based on the effect of electromagnetic induction. Therefore, a magnet and a coil | Electromagnetic energy harvesting is based on the effect of electromagnetic induction. Therefore, a magnet and a coil are used to generate a current. The design can be very simple. In rotating machine elements, like a splined shaft, a commercial DC-motor can be used.<ref name="Quanz2023" /> | ||
===== Radiofrequency energy harvesting ===== | ===== Radiofrequency energy harvesting ===== | ||
Radiofrequency(RF) energy harvesting is based on receiving and rectifying RF energy. This can be passive harvesting using environmental energy or active transmission like in RFID readers. Common frequencies used are 434 MHz, 868 MHz and 2.4 GHz. | |||
=== Energy storages === | === Energy storages === | ||
Examples for energy storages that were integrated into SiME within the SPP 2305 are: | |||
* 7.4 V Li-Ion 3000 mAh (50h continuous high speed measurement, > 250 h discontinuous measurements) | |||
* ET1210C-H 4mAh (12.5x1.3mm, deep discharge, constant voltage charging, reflow solderable, up to 105℃ operating temperature | |||
=== Processors (in situ) === | === Processors (in situ) === | ||
Examples for processors used for in-situ measurements in SiME within the SPP 2305 are: | |||
* STM32U5xxx | * STM32U5xxx (Relatively low power, but offers high processing power (Cortex M33); fast, efficient ADC (2.5 MSPS at 1 mA)) | ||
* PSOC 6 CY8C63xxx (Low Power MCU, dual ARM CPU (M0+ for controlling, M4 for data processing), BT LE 5.0 subsystem, multi-channel ADC (1 mA @ 1 MSPS), programmable analog subsystems) | |||
* BGM220S (Low Power MCU (<200nA Deep Sleep), Cortex M33, BLE 5.2, Integrated RF-Frontend+Antenna, Wakeup through RF Signal in Deep Sleep) | |||
=== Methodology for design of SiME === | === Methodology for design of SiME === | ||
Line 318: | Line 344: | ||
[[File:Modulbaukasten.png|thumb|alt=Modulbaukasten|Idea of a modular system for the development of SiME by configuration]] | [[File:Modulbaukasten.png|thumb|alt=Modulbaukasten|Idea of a modular system for the development of SiME by configuration]] | ||
SiME can be understood as mechatronic or cyber-physical systems (CPS) due to their mechanical, electrical and information technology components. The development of mechatronic systems can be methodically supported. The VDI guideline VDI2206 for the design of mechatronic systems uses the V-model as a central development tool. In the V-model, discipline-specific solutions are developed based on the requirements and checked through verification and validation activities in the form of tests and simulations. A V-model adapted to the development of modular product architectures can be seen | SiME can be understood as mechatronic or cyber-physical systems (CPS) due to their mechanical, electrical and information technology components. The development of mechatronic systems can be methodically supported, e.g. by the V-Model. The VDI guideline VDI2206 for the design of mechatronic systems uses the V-model as a central development tool. In the V-model, discipline-specific solutions are developed based on the requirements and checked through verification and validation activities in the form of tests and simulations. A V-model adapted to the development of modular product architectures can be seen [[Index.php?title=Media:V Modell PKT.png|here]] <ref>Küchenhof, J., Berschik, M. C., Heyden, E., & Krause, D. (2022). Methodical support for the new development of cyber-physical product families. ''Proceedings of the Design Society'', ''2'', 495-504.</ref>. | ||
==== Low level support for development of SiME ==== | |||
Most methodologies for support of development are designed to support on a high level level only. Low level support for SiME as specifications for the established methodologies are needed to support development. The projects within the SPP 2305 can provide the specifications through best practices and learnings. | |||
As an example a procedure for sensor integration into cylindrical machine elements is currently being developed. Support on a low level can include e.g. best practices on how to identify the design space for the sensors, how strain gauges can be identified and how to reproducibly apply them on a structure. Also wiring issues and temperature compensated electrical design are learnings that are provided by projects within the SPP 2305. | |||
==== Modular system ==== | ==== Modular system ==== | ||
The idea of a modular system is to be able to create products by combining modules. For SiME, this means being able to create application-specific system configurations of microelectronic components and modules for sensor systems for SiME with minimal effort. Depending on the ME and application, suitable components and modules are selected and configured into a compatible overall system, which is then integrated into the respective ME in a space-neutral manner without impairing the primary function. | The idea of a modular system is to be able to create products by combining modules. For SiME, this means being able to create application-specific system configurations of microelectronic components and modules for sensor systems for SiME with minimal effort. Depending on the ME and application, suitable components and modules are selected and configured into a compatible overall system, which is then integrated into the respective ME in a space-neutral manner without impairing the primary function. | ||
[[Index.php?title=Media:Modulbaukasten.png|The figure]] shows this schematically by equipping various ME such as a gear wheel, ball bearing, screw or feather key with an integrated sensor system and thus becoming a SiME. The sensor systems require basic modules for their functionality to fulfill their respective measuring task, suitable data processing and successful energy management.[[File:Modular system scheme.png|alt=Modulbaukasten nach Dambietz|thumb|303x303px|Schematic overview of the structure and linking of input data and configuration data]][[File:Configuration Network Diagram.png|thumb|alt=Configuration Network Diagram|Configuration Network Diagram]]A methodical procedure for developing a configurable modular system is shown schematically [[Index.php?title=Media:Configuration Network Diagram.png|here]]. The procedure mainly consists of a data input and two associated methods. First, the product architectures are implemented in SysML. Then, the configuration system creates a sensor system based on boundary conditions and compatibility issues. The individual product/ system variants generated on the basis of the various product architecture alternatives are then evaluated based on performance criteria. | |||
Configuration network diagrams are created for system synthesis. The product properties are linked to the components and the components are assigned to the respective modules. The overall structure can then be implemented in SysML. | Configuration network diagrams are created for system synthesis. The product properties are linked to the components and the components are assigned to the respective modules. The overall structure can then be implemented in SysML. | ||
For the implementation in SysML a hierarchical structure is followe which can be accessed via package diagrams. The V-model serves as a Meta-metamodel inihibiting the metamodels and the models. The metamodels are dependency matrices which connect different model types. The models themselves represent the lowest modeling level. | For the implementation in SysML a hierarchical structure is followe which can be accessed via package diagrams. The V-model serves as a Meta-metamodel inihibiting the metamodels and the models. The metamodels are dependency matrices which connect different model types. The models themselves represent the lowest modeling level. | ||
In SysML, individual diagrams can be created separately, which are arranged along the V-model as shown here. Different diagram types can be used in SysML, such as requirement or block diagrams, in which the product properties, components, modules and module variants can be mapped. The individual diagrams can be linked by dependency matrices. In this case, requirements are linked to product properties, properties to components, components to modules and modules to module variants. An exemplary hierarchical requirements diagram is shown [[Index.php?title=Media:Anforderungsdiagramm hierarchisch.png|here]]. | |||
In the project sensor-integrating bolt for multi-axial force measurement a modular electronics architecture realized as a flex pcb with interfaces to swap the module for data and energy transfer was developed. This enables an adaptation to different environmental settings, e.g. bright and dark environments (solar panels) or electromagnetic interferences (HF-technology).[[File:Hierarchy levels.png|thumb|Hierarchical modeling levels of the model-based ''Modular Building Kit'' |406x406px]] | |||
[[File:SysML V Modell filled.png|thumb|alt=SysML V Modell filled|SysML V Modell filled]] | [[File:SysML V Modell filled.png|thumb|alt=SysML V Modell filled|SysML V Modell filled]] | ||
Line 341: | Line 371: | ||
=== Costs of electronic components === | === Costs of electronic components === | ||
The cost of the electronic components | The cost of the electronic components differs typically by their specification. By the integration of sensors, the cost of the machine element are rising. These costs can be compensated by added value of reliability and availability of the monitored machine element. | ||
==== High-quality ==== | ==== High-quality ==== |
Latest revision as of 20:58, 14 October 2024
Introduction
Caused by Industry 4.0 and the implementation of cyber-physical systems, a significant demand for high-quality and reliable information about relevant state and process variables of technical systems arises. Sensor-integrating machine elements (SiME) offer great potential in this context since they enable the measurement of these variables directly at or close to their point of origin, so-called in-situ measurement. SiME build upon the primary mechanical functions of conventional machine elements and extend them by sensory functions. For SiME, the measurand - the quantity to be measured - is directly affected by the primary mechanical function of the machine element and measured by integrated sensors. Since the interfaces of the conventional machine elements are maintained and almost no additional installation space is required, SiME can easily be retrofitted into technical systems that were not developed against today's background. This means that also older technical systems can be made usable and continue to be operated in the context of Industry 4.0, which is particularly advantageous from an ecological point of view.[1][2]
Consequently, SiME can pave the way for widespread digitalization. However, to fulfill this vision, a varity of new and innovative SiME are needed. Therefore, the German Research Foundation (dt. Deutsche Forschungsgemeinschaft, DFG) funded the priority program (dt. Schwerpunktprogramm, SPP) 2305. The goal of the SPP is the development of various SiME. In the following, the results and findings of the ten projects conducted within the SPP 2305 are outlined in the form of a wiki. The projects of the SPP 2305 are:
- Auto-informative plain bearings
- Elastic couplings with integrated flexible dielectric elastomer sensors
- Integrated sensors for intelligent large-size bearings
- Load sensitive splined shaft with sensory material
- Microelectronic modular system for sensor-integrating machine elements
- Sensor-integrating machine element radial shaft seal for monitoring of operation conditions and lubricant quality
- Sensor-integrating feather keys for the detection of torques
- Sensor-integrating gear
- Sensor-integrating bolts for multiaxial force measurement and derivation of a design methodology for sensor integration in closed cylindrical machine elements
- Standardized integral instrumentation of gas foil bearings for condition and operation monitoring
Exemplary measurement tasks in machine elements
In the following, exemplary measurement tasks and their respective quantities of interest are described for the machine elements that are considered in the respective projects within the SPP 2305.
Gear
Gears are usually subject to a standardized design process (ISO 6336[3]), with a variety of power levels (e.g., wrist watches to wind turbines). Since gears are relevant for the functionality of the overall system, detecting gear faults as early as possible is benefitial. A measurement at or in the gear is of interest because of the damping of the elements from the gear to the housing, which is the typical measurement position.
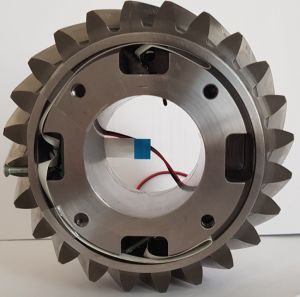
The physical quantities relevant for the primary function of the gear operation are:
- instantaneous rotational speed
- torque
- temperature
- excitation behaviour
Other relevant physical quantities include:
- type of lubrication
- lubrication quality
- gear material
- gear geometry
Thus, for an efficient monitoring of gears the following physical quantities are beneficial to be measured:
- torsional acceleration[5][6][7][8][9]
- lubrication thickness in the loaded contact
- instantaneous rotational speed
- gear temperature[6][7]
- structure borne noise
Depending on the assembly into the gearbox and the type of gear (spur gear or helical gear) different designs are possible which are also depending on classical designs of microelectronic circuits. So, for gears the following two designs are most relevant:
- circuit board on the side plane of the gear
- axial cavities (possible for helical and spur gears, better suited when press fit is used instead of feather key, more interaction with mechanical operation of the gear)
Bolt
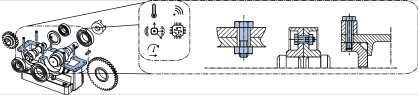
Standardized metrical bolts according to ISO 4014 and dimensioned according to VDI 2230 are the most widely used machine elements. Positioned in the load path, they offer excellent potential for driving digitalization through the procurement of in-situ data. Therefore, in addition to measure physical quantities that are directly related to the primary function, it is also possible to measure a range of other physical quantities. The physical quantities relevant for the primary function are:
- torque (from tightening)
- axial force
- bending torque
Other physical quantities that can be measured include:
- temperature
- acceleration
Sensor-integrating bolts exist in the state of the art, e.g. the following:
- PiezoBolt from ConSenses
- SmartScrew from sensorise
- Q-Bo from Fraunhofer IIS
Most of the existing solutions however do not fulfill the requirements of this SPP 2305. Sensors and electronics need to be fully integrated into the bolt and self-sufficient in order to maintain usability as the conventional bolt. The integration of sensors and electronics for energy delivery and processing requires sufficient design space inside the bolt. Any removal of material does however weaken the primary function. This leads to a conflict of objectives between the mechanical function (clamping force - load carrying capacity) and the sensory function (acquiring measurements with a high quality). This conflict needs to be solved by the help of models and analyses. The inevitable loss of load capacity can partly be compensated by changing the bolt's material strength class.
Rolling bearing
Rolling bearings play a central role in the world of machine elements. These inconspicuous yet extremely vital components are indispensable in a wide range of industrial applications, whether in automotive drive systems, wind turbines, huge turbines in power plants or in the precise mechanisms of state-of-the-art robot technology. Rolling bearings enable low-friction movement and transmit forces efficiently, making a significant contribution to the performance and reliability of a wide range of machines.
As digitalization progresses, the integration of digital technologies in a rolling bearing opens up new possibilities for monitoring and optimization. By implementing condition monitoring systems, data can be collected, analyzed and interpreted during operation to monitor the condition of a rolling bearing in real time.
These systems use a variety of sensors to record parameters such as temperature, vibration, lubricant condition and load. In particular, the use of thin-film sensors on the bearing disk of a rolling bearing can be used to detect temperatures or acting forces directly in the effective zone of the bearing. The collected data is then evaluated using algorithms and analysis techniques to detect potential anomalies or deviations from normal operation at an early stage. This allows maintenance intervals to be optimized, downtimes to be minimized and preventive maintenance measures to be planned.
Physical parameters that can be measured:
- temperature
- strain
- rotational speed
- vibration
- lubricant condition
The condition monitoring of rolling bearings is therefore a key element in the predictive maintenance of machines and technical systems. It enables a proactive approach for maintenance by providing operators and engineers with important insights into the current condition of the bearings. By detecting wear, damage or other problems in good time, expensive repairs can be avoided and the service life of the machines can be extended. In an increasingly digitalized world, condition monitoring therefore plays a crucial role in ensuring the efficiency, reliability and cost-effectiveness of industrial processes.
Gas foil bearing
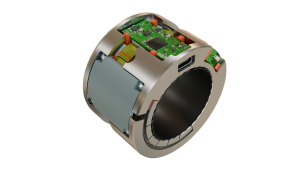
Gas foil bearings (GFBs) are an advanced class of fluid dynamic bearings that utilize a thin layer of gas, typically air, as a lubricant in a gap between a rotating journal and an elastic metal foil structure, consisting typically of a supporting bump foil and a smooth top foil. This design allows for the creation of a load-bearing gas film at operational speeds, effectively minimizing friction and wear by maintaining separation between the rotor and bearing surfaces through dynamic pressure in the lubrication film. The compliant foil structure enables adaptability to varying operational conditions without the need for tight radial clearances. GFBs are thus able to function at large rotating speeds with high efficiency, low maintenance and without oil and related problems. GFBs are thus particularly suited for applications in high-speed rotating machinery where oil lubrication is undesirable or impractical, including but not limited to fuel cell blowers, air cycle machines, microturbines, and compact compressors.
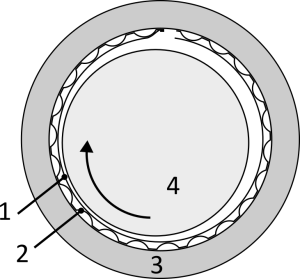
Despite their advantages, GFBs can be susceptible to strong subharmonic vibrations, similar to those encountered in other hydrodynamic bearings. In addition, they may suffer from thermal instability, leading to unstable operation due to the different thermal expansion of different GFB components. The integration of sensors within GFBs for real-time monitoring of operational conditions will allow controllers to better adress these challenges. The most relevant measurement quantities in this regard include:
- vibrations
- temperature (fields) in bearing components and gas film
- location of the rotor
Further quantities that may be deduced or measured within a GFB include:
- pressure (fields) in the gas film
- gas composition, water content
- rotational velocity of the rotor
- orbit of the rotor
- current lubrication regime
Plain bearing
Besides roller bearings, plain bearings are the most frequently used machine elements in mechanical engineering, which enable the relative movements of machine parts to each other. A plain bearing, or more commonly sliding contact bearing and slide bearing, is the simplest type of bearing, comprising just a bearing surface and no rolling elements. Therefore, the journal (i.e., the part of the shaft in contact with the bearing) slides over the bearing surface. The simplest example of a plain bearing is a shaft rotating in a hole. The effects of bearing damage are serious in economic terms as well as in terms of safety. Consequently, condition monitoring of bearings is becoming increasingly important to minimize downtime. Plain bearings are characterized by having a longer service lifetime and higher load capacity at equivalent dimensioning compared to roller bearings[10]. Therefore, plain bearings are especially suitable for long-term and heavy-duty applications. Accordingly, roller bearings are increasingly being replaced by plain bearings in the planetary stages of wind turbine gearboxes[11]. Additionally, first concepts of main drive trains with plain bearings in wind turbines have been published[12],[13]. In summary, significant challenges for the safe and economical operation of a drive train can be identified: The severe effects of bearing damage in drive train systems and the current development trends leading to higher loads and increased use of plain bearings in drive trains.
Regarding the type and direction of the forces occurring between the moving machine elements, a distinction is drawn between statically or dynamically loaded radial and axial plain bearings[14]. Furthermore, a distinction between plain bearings without the use of an intermediate medium, which are permanently subject to wear, and those with a separating medium (typically oil) can be made. Plain bearings using a separating medium are advantageous in terms of their friction behavior, which can be optimized to the extent of no wear occurring during operation. However, the wear-free state can only be ensured if solid contact between the two contact partners, the bearing bush and the shaft, is completely avoided. Plain bearings, which are operated using a separating medium and therefore can enable wear-free operation, are classified into hydrostatic and hydrodynamic plain bearings[15]. In case of hydrostatic plain bearings, the wear-free state is achieved by applying pressure to the lubricating film externally by a pump. Therefore, the state of motion created, does not influence the separation of the surfaces relative to each other. In the case of hydrostatic plain bearings, the lubrication gap height can be controlled by using active hydraulic chamber systems [16],[17],[18]. Due to active separation of the wear surfaces, sensor-integrated condition monitoring is of secondary relevance for hydrostatic plain bearings. The friction and wear behavior of the surfaces moving relative to each other in hydrodynamic plain bearing is decisively dependent on their relative speed. Wear-free conditions are only achieved at sufficient relative speed. Hydrodynamic axial plain bearings, which primarily support axial forces in the direction of the shaft, are used less frequently compared to radial hydrodynamic plain bearings. Accordingly, the following section will focus primarily on hydrodynamic radial plain bearings and the possibilities for condition monitoring.
For monitoring hydrodynamic radial plain bearings, the measurement of a number of quantities is well established. Possibly used monitoring principles are:
- temperature monitoring
- acoustic emission
- lubricant monitoring
- friction torque
- orbital analysis
- electric contact resistance
- acceleration monitoring
Shaft coupling
Couplings are mechanical elements that connect two shafts in order to transmit mechanical power from one to the other. Furthermore, they i) can compensate for shaft misalignment, ii) have a switching function to interrupt or limit the power flow, and iii) compensate for shocks. The industry provides a variety of application-specific designs, which satisfy diverse requirement profiles. VDI 2240 provides a suitable basis for selecting and classifying couplings according to their requirements. A subdivision is made according to switchable (clutch) and non-switchable (couplings) couplings. Based on this classification, different possible measurement quantities result. For couplings, the measured variables of a torque and rotational speed are particularly relevant. Furthermore, temperature, wear, shaft misalignments, restoring and reaction forces, and vibrations can be significant. For clutches, which also includes brakes, the measurement of the same parameters is desirable. Additionally, relevant parameters are clutch engagement and slip between the two hubs. [1]
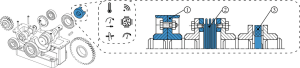
Important features that are of interest for these machine elements are:
- torque,
- rotational speed,
- temperature,
- shaft misalignment and
- vibration
An important subclass of couplings are elastic couplings such as jaw couplings. They can be used to compensate for shaft misalignments and can mitigate critical torque shocks. Couplings are ideal components for measuring process data as they are located directly in the power flow.
Splined shaft
Splined shafts are a shaft-hub connection that are used to transmit torque. Splined shafts are standardized machine elements according to DIN 5480 and ISO 4156. As splined shafts are located directly in load path of machines, they are suitable as a sensor-integrated machine element for making statements about the operating status of the machine and the experienced loads. The main type of load is torsion, but other load cases with additional bending moment or shear force can occur.
The physical quantities relevant for the primary function are:
- torque
- bending torque
- fit of the teeth
The physical quantities are beneficial to measure:
- torque
- rotational speed
- temperature
Feather key
Seltmann et al. [1]developed a feather key (FK) for measuring the circumferential force by means of topology optimization, where the main dimensions are based on DIN 6885. The main idea is as follows: The FK is normally subjected to a non-uniform surface pressure, which, in addition to the torque, also depends on the hub geometry, resulting in a complex deformation of the FK. In order to determine the resulting circumferential force from this deformation field, the deformation of the FK must be measured with a large number of strain gauges. This is followed by complex calculations to determine the resulting circumferential force. With the aid of topology optimization, however, the geometry of the FK is adapted so that it always deforms approximately according to a linear combination of a few deformation modes under different non-uniform surface pressures. This reduces the number of strain gauges required to the number of deformation modes and simplifies the calculation of the resulting force. The boundary conditions were simplified for the topology optimization. For testing under practical boundary conditions, the geometry of the stiffness conditioned FK was simplified and a finite element model was created, as shown here. For showing differences in pressure distribution dependent on the hub geometry two different cases are simulated. A torque is applied, and the deformation of the FK in the numerical model is studied. It is shown that the deformation can be described by a linear combination of two deformation modes, so the deformation of the FK should be measurable by applying two strain gauges.
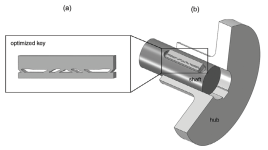
The most relevant physical quantities are:
- torque
- shear stress
- bearing stress
- material properties
- key dimensions (width, height, length)
Seal
Seals are widespread machine elements for separating adjacent areas between which an exchange of substances is to be suppressed to a desired extent. In addition to the seal itself, a sealing system therefore also includes the interacting counter surface as well as the media applied.
In the case of a rotary shaft seal used at shaft exits from machine housings, shaft rotation causes a relative motion between sealing lip and counter surface. As a consequence, an active sealing mechanism evolves in the sealing contact, enabling the lubricant to be pumped towards the oil sump. Within this context, the proper sealing function depends on the interaction of various ambient and operational parameters, whose knowledge enables conclusions about the condition of the sealing system.
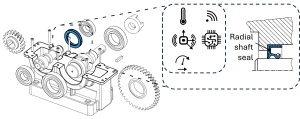
Since there are no reliable methods for prediction of a rotary shaft seal’s service life[1], Thielen et al. proposed sensor integration approaches aiming for in-situ measurement of several parameters, particularly those related to the sealing mechanism[19]. These include:
- oil sump temperature
- oil sump pressure
- lubricant quality
- sealing contact temperature[20]
- sealing contact friction (friction torque)[21]
- sealing lip preload[21]
The sensor system's power supply as well as data transmission are realised wirelessly so that the rotary shaft seal can also be retrofitted to existing machines.
Interaction of sensor system and machine element
Calculation methodology for service life / load carrying capacity
Gears
Involute gears have a standardized set of defining parameters which may be found in ISO 21771. The gear geometry of the vast majority of gears made from steel for small, medium and large applications is defined according to that standard. Load carrying capacity for these gears is analyzed by the methodology defined in ISO 6336. Gear failures may be distinguished in pitting, tooth root breakage, micro-pitting, scuffing, tooth flank breakage and wear. The methodology for each failure mode is briefly characterized in the following:
Pitting damage is a local material breakout of the active tooth flank. As a characteristic value the tooth contact pressure is calculated and the safety factor or fatigue life may be derived. The S-N-curve for the gear needs to be defined, e.g. in relation to the material and heat treatment applied.
Tooth root breakage is a breakout of one or more teeth starting in the tooth root fillet. As a characteristic value the tooth root stress is calculated and the safety factor or fatigue life may be derived. The S-N-curve for the gear needs to be defined, e.g. in relation to the material and heat treatment applied.
Micro pitting is a continuing breakout of very small particles out of the active tooth flank . As a characteristic value the relative lubricating film thickness in tooth contact is used and a safety factor or a lifetime may be derived. The limit is not defined by an S-N-curve but by a reference value of required minimal lubricating film thickness.
Scuffing is a local welding of the meshing tooth flanks and a consecutive separation. As a characteristic value the contact temperature in tooth contact is used and a safety factor may be derived. Scuffing is characterized as an instantaneous damage and therefore not decribed by an S-N-curve.
Tooth flank breakage starts as a crack of the tooth flank beneath the surface and a successive crack propagation through the whole tooth until breakout of the upper part of the tooth. Characteristic value is the equivalent stress in the tooth in comparison to the stress limit.
A documentation of the path of calculation may be found in ISO 6336 and is not given in detail here.
Bolts
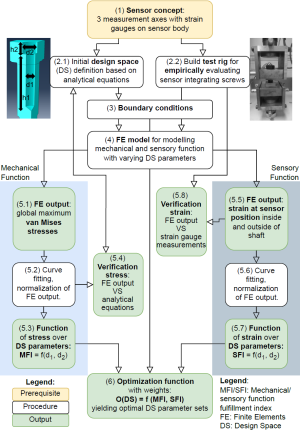
Bolts are standardized in geometry according to ISO 4014 and dimensioned according to VDI 2230. An objective for the sensor integration is to maintain the load carrying capacity as much as possible while providing a sufficient measurement quality. This usually leasds to a conflict of objectives in many machine elements, because the sensory function needs space inside the machine element, that is also needed for providing the mechanical function. Especially for bolts this is a problem, because the design space is rather small.
For bolts, an optimization function is necessary that optimizes the design space while taking the mechanical and sensory function into consideration. The mechanical function can be evaluated by the change in v. Mises stress, the sensory function needs to be modelled according to the sensors used.
Feather keys
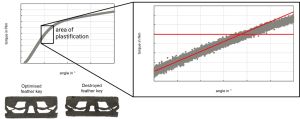
The fatigue strength of a feather key connection can be calculated by different concepts. On the one hand, the fatigue strength of the notched shaft can be carried out by the German national standard DIN 743 and on the other hand, the transmittable torque can be calculated by the German national standard DIN 6892, which addresses the pressure distribution between the feather key and the shaft notch and the pressure distribution between the feather key and the hub notch. This standard is divided in three methods, of which method C is relevant in the context of sensor-integrating feather key connections. In the elastic deformation range, there is a linear relationship between torque and angle of twist. When the key is plastically deformed, the relationship between torque and angle becomes non-linear, as shown by the evaluation of a quasi-static test in the right-hand side figure.
Since the concept of calculating circumferential forces is based on the theory of linear elasticity, the sensor-integrating feather key must not show any plastic deformation. The corresponding threshold value for the transmittable torque can be estimated using method C of DIN 6892, where a critical pressure , the height of the feather key and the supporting height in the “critical” notch , the supporting length , the number of feather keys , the supporting factor and the shaft diameter are taken into account. The transmittable torque is given by
.
Mechanical integration
Prototypes
In order to test the developed concept it is important to start with the production of prototpyes as early as possible to gain a better understanding and to mitigate or even detect the amount of possible failure modes. In this way, possible errors that were not previously thought of can be identified. Hence prototypes serve as testing objects to gather knowledge about the function behaviour structure connection.
Wiring / connectors
When cables are used inside a machine element they are subjected to´(i) cyclic strains or (ii) very high strains and stresses. It follows that they often break down. In order to eleviate this problem, micro coaxial cables can be used.
Testing / validation
Continuous testing of new components is essential during the development of SiME. This reduces the risk of errors accumulating. Ideally, the individual components are tested separetly at the beginning. This speeds up the process and errors can be detected accuratly and early.
Testing includes the question how the SiME performs under developing damages. This poses several challenges: Not only have the sensors to be robust enough to resist often harsh conditions for damaging the machine elements. Also several SiMe have to be available for testing and potential destruction by the test. Furthermore an adequate test rig to apply realistic operating conditions to the specimens has to be available. All this leads to the fact that the first tests of the campaign are mostly measurement tests and only later in the project test conditions will become more challenging and related to real operation of the SiME.
Operating strategy
Data handling
The amount of data generated by SiME depends on the employed sensor principle and the data acquisition frequency. The strategy for the handling of this data will also have to be informed by other boundary conditions, such as the limitation of the communication system and the energy required to store, process and transfer the data. Important concepts for dealing with the data are algorithmic reduction and buffering. The former reduces the amount of data that has to be handled through processing. The latter deals with concepts for the temporary storage of data before further steps can be taken.
Algorithms for reduction
Data processing methods: one of the most efficient ways to compress data may be to calculate the target values directly from them, reducing the data to only the relevant information of interest.
Since many fault detection approaches still rely on external high-performance measurement systems unsuitable for in-situ integration, algorithms for damage detection have to be adapted for low-power embedded systems, such as Microcontrollers (MCUs). Moreover, the minimum required data sample rate necessary for damage detection needs to be determined in order to acquire data in the most efficient way, which can be, for example, achieved by using a downsampling approach. One typical use case for data reduction is gear condition monitoring, which can prevent unexpected downtimes or sudden failure of machinery [22].
Methods for buffering
Ringbuffer / FiFo: A type of buffer, where a new element is always written over the oldest element in the buffer. That means its purpose is to always preserve the most recent data written.
When implementing any of these techniques, the choice of memory location is crucial: in RAM the data is more easily accessible and consumes less power for writing / reading, but the memory is volatile and the data will be lost on power loss. This type of buffer can also be directly implemented in digital sensors, allowing the host processor to retrieve batches of data at longer intervals. In non-volatile memory like Flash / EEPROM the data will persist in case of power loss, also larger storage sizes are available, but the reading and writing consumes more power.
Outlook on the use of data
The ultimate goal for most sensor-integrated machine element applications is condition monitoring of the element itself, nearby components or a machine assembly as a whole. This has to be taken into account when designing a data handling strategy.
However, in research applications it is often necessary to first collect more extensive preliminary data to learn about the underlying degradation process. Only after the data generating process is understood a fitting data handling strategy can be designed that will efficiently handle the information while preserving the characteristic patterns for later examination.
Operating strategy for processors
The operating strategy, the strategy for when to do what, is a key factor in the power consumption of the system, because the processor is one of the components with the highest consumption of any system. The choice of operating strategy is largely dependant on the task of the system. A general rule is that it the processor should be active only as often as necessary.
Continuous
The processor operates continuously, without reverting to sleep modes. This consumes the most power.
Duty Cycle
The processor operates on a schedule and reverts to a low-power mode in between the active phases. This can be realized using timer interrupts. In some modes, peripherals may be active while the processors are not, collecting or preparing data for the active phase.
Eventbased
The processor operates after an event has happened. This can be realisrealizeded using interrupt signals from either internal hardware like comparators or external hardware, like additional sensors.
Data transfer
Barriers / shielding
Since electromagnetic waves are shielded and reflected to some extent by metal, the integration of sensors in metallic machine elements poses a challenge for communication. However, contrary to common perception, it is possible to send data out of a fully enclosed metal case. Real metal has finite resistance, and the magnetic field component can penetrate a faraday cage, leading to strong damping (about >50dB).
An alternative approach to transmit data in or out of a metallic machine to communicate with the SiME can be achieved by using ultra sonic waves. Those waves can penetrate through metal with little dampening. This approach is used in a variety of applications [cite] and can be adapted for the use in machine elements.
Protocols
Long Range Wide Area Network (LoRaWAN) is a low-power wireless network protocol operating at the network layer. It is defined by the LoRa Alliance and provides specifications that are freely available. Additionally, software building blocks are accessible as open-source software.
The architecture of LoRaWAN is star-shaped. LoRa end devices communicate with LoRa gateways, which then forward the data packets to a LoRaWAN server. This server interfaces with IoT platforms and applications. Communication within LoRaWAN is doubly encrypted using 128-bit AES, both from the end device to the network server and from the network server to the application server.
LoRa end devices and gateways in LoRaWAN utilize a proprietary and patented transmission method based on a chirp spread spectrum modulation technique called “LoRa". LoRa operates at the physical layer and is asymmetrically designed for energy efficiency, achieving uplink communication ranges of over 10 km. Data rates range from 292 bit/s to 50 kbit/s. Various operational modes, including quasi-continuous downlink communication, are possible, although the latter affects energy efficiency. The LoRa Alliance also refers to this technology as Low Power Wide Area Networks (LPWANs). LoRa uses different regional frequency bands in the ISM and SRD bands. For example, in Europe, the frequency band ranges from 433.05 to 434.79 MHz (ISM Band Region 1) and from 863 to 870 MHz (SRD Band Europe). The coverage extends from 2 km in urban areas to 40 km in rural regions. Notably, LoRa’s penetration capabilities allow it to reach even basement areas [23].
Other protocols that can be used in the context of SiME are:
- Bluetooth Low Energy
- Zigbee
- Mioty
- Sigfox
- NB-IOT
Validation strategy
A crucial step for the evaluation of an operating strategy is the assessment of algorithm execution time, especially when using low-power embedded microcontrollers. If the execution time of selected algorithms cannot meet the timing requirements of a specific use-case considering them in the operating strategy is not feasible. Thus, it is important to consider algorithm execution time right from the beginning of the system design. Thereby, performance benchmarking methods provide tools to effectively measure and predict algorithm execution time within the design process [24]. For early design states, early-stage execution time prediction approaches, for example, based on sparse measurements can give a first estimate about algorithm execution times on different hardware devices by simultaneously minimizing measurement effort [25]. Challenges in measuring software execution time on heterogeneous devices can be mitigated by a systematic selection of execution time measurement methods within the benchmarking setup [26].
Microsystem technology
Sensor systems
Intelligent sensor systems, that are used to measure a variety of different measurands, are relevant examples for microsystems in the context of SiME. In these sensor systems, signal processing is moving ever closer to the point of measurement, resulting in decentralized, independent systems[27]. Sensor systems in the context of microsystem technology are characterized by different aspects:[28]
- small size, mass and minimal energy consumption of the system,
- high reproducibility of the system parameters in production,
- compensation of environmental influences and cross sensitivity through localization of sensors and signal processing in the smallest possible space,
- material and cost savings through parallel production of large quantities and
- high reliability through integration, reduction of interferences by reducing electrical contacts and cables.
Overview of measuring principles
The measuring principle is defined according to the Joint Committee for Guides in Metrology (JCGM) and the German Institute for Standardization (dt.: Deutsches Institut für Normung (DIN)) as phenomenon (physical, chemical or biological) serving as a basis of a measurement. The measuring principle allows another variable to be measured instead of the measurand to determine the value of the measurand from its value. It is based on a physical, chemical or biological phenomenon or effect that can always be reproduced with a known law between the measurand and the measurand variable. In the following, different measuring principles for measurands relevant in the context of SiME are outlined, whereby the focus is on physical phenomenons.[29][30]
Temperature
Temperature can be measured using three different principles:
- silicon Bandgap: this type of sensor depends on the temperature dependence of the forward voltages of diodes. It is used in most temperature sensors in integrated curcuits, since it can be easily integrated into silicon wafers. Sensor-Examples: TI TMP119 (0.08°C accuracy, 5 µA at 1.7 - 5.5 V)
- seebeck / thermoelectric effect: The voltage is produced between different metals if they are contacted at different temperatures. These combinations are called thermocouples.
- resistance: the electric resistance of resistors changes with temperature. Therefore, the resistance of certain materials like platinum can be used as temperature sensor. Todo so a resistor made out of platinum with the addition of other elements for long-term stability can be used.
Strain
Strain can be measured using several approaches:
- strain gauges
- piezo elements
- dielectric elastomer sensors (DES)
With known material properties, the acting load can be derived from the measured strain. However, most approaches to strain measurement have different sensitivities depending on the direction of the strain. It is advantageous to use a deformation body that decouples the acting components to different strain ranges, if more than one force component is to be measured. Ideally, a sensor designed to measure three forces would have three distinct zones where the strains respond proportionally to only one force component each. In some cases, the use of Wheatstone bridge circuits can help to reduce cross-sensitivity[31][32].
Vibration
Vibrations, acceleration, respectively, can be measured using several measuring principles:
- capacitive (MEMS)
- piezo-electric
Electromagnetic sensors
Electromagnetic testing methods include a wide variety of testing techniques. Typical methods are the impedance method, conventional eddy current testing and magnetic inductive testing. At least one coil is required for electromagnetic testing. In addition to the exciter coil, a measuring coil and a compensation coil can be added. If the electrical conductivity and/or the magnetic permeability of the test object changes, this can be detected non-destructively on the basis of the signal change [33]. For instance, in combination with an austenitic metastable stainless steel, overloading of the component can be detected. The measuring effect is the transformation of paramagnetic austenite into ferromagnetic martensite when a certain load is exceeded [34].
One way of measuring large strains is to use dielectric elastomer sensors (DES) [35]. They consist out of a dielectric layer which is sandwiched between two compliant electrodes. An electric field will form if an electric potential difference is applied on the two electrodes and a capacitance can be measured. Electrically, DES behave like plate capacitors. A deformation of the DES leads to a change in the capacitance which can then be used to measure the strain or force that caused this deformation.
Robustness and Resilience
The robustness and resilience of the sensor system are crucial for its proper function, even in the presence of disturbances, as well as the reliability of the measuring data provided by a SiME. Therefore, disturbances that may occur in the later use context of the SiME must be identified and considered early on in its development.
On the one hand, robustness and resilience must be taken into account when selecting components and modules for the sensor system, e.g., sensors. Sensors can rely on different measuring principles, physical effects, respectively, that change the measurand into an electric measuring signal. These effects may be more or less susceptible to disturbances occurring in the later use context of the system. Hence, it is reasonable to select components that are less susceptical to disturbances occurring in the later use context of the SiME. Since not all manufacturers provide the information required to conduct this selection, experimental benchmark and functional tests are a suitable approach for obtaining this information.
On the other hand, robustness and resilience must also be taken into account when the sensor system is verified or tested. In this context, early verifications and testings of the individual components and modules of the sensor system in the later environment, e.g. in oil, was found to be a promising approach by many projects. In order to protect the sensor system and susceptible modules from disturbances, different approaches can be chosen, e.g. an encapsulation or shielding of the components or modules. Mathias et al.[36] cluster these different approaches based on their point of attack in the cause-and-effect chain into three so-called Robust Design strategies: elimination of disturbance, elimination of disturbance influence and elimination of disturbance impact.
Energy harvesters
Different types of energy harvesters can be used to extract energy from the environment. [37] gives an overview of different energy harvester types. Typical energy harvesters are:
Piezoelectric energy harvesting
Piezoelectric energy harvesters comprise a piezoelectric element, its mechanic fixation and electronics. When the piezoelectric element experiences mechanical stress it produces a charge. This charge is then rectified and converted to the needed voltage by the electronics. Piezoelectric harvesters are not available as premade products but have to be constructed custom for each application, since their construction depends on the amplitude, direction and frequency of the stress. The core is formed by a premade piezoelectric element that is sensitive to stress in the right direction and at the right frequencies, the mechanical fixation is then built around it to maximize the stress and amplitude.
Thermoelectric energy harvesting
Thermoelectric energy harvesting is a method for capturing energy in processes by utilizing temperature differences and converting them to electrical energy[38]. Thermogenerators (TEG) are devices that utilize occurring temperature differences and convert those temperature gradients into electricity based on the thermoelectrical effects[39]. Thermoelectric harvesting is an emerging technology, which is increasingly explored and further developed regarding its efficiency and reliability[40][41][42]. This also includes the low-level heat range, in which the TEGs are able to harvest energy at occurring temperature differences of a few Kelvin[43][44].
Electromagnetic energy harvesting
Electromagnetic energy harvesting is based on the effect of electromagnetic induction. Therefore, a magnet and a coil are used to generate a current. The design can be very simple. In rotating machine elements, like a splined shaft, a commercial DC-motor can be used.[45]
Radiofrequency energy harvesting
Radiofrequency(RF) energy harvesting is based on receiving and rectifying RF energy. This can be passive harvesting using environmental energy or active transmission like in RFID readers. Common frequencies used are 434 MHz, 868 MHz and 2.4 GHz.
Energy storages
Examples for energy storages that were integrated into SiME within the SPP 2305 are:
- 7.4 V Li-Ion 3000 mAh (50h continuous high speed measurement, > 250 h discontinuous measurements)
- ET1210C-H 4mAh (12.5x1.3mm, deep discharge, constant voltage charging, reflow solderable, up to 105℃ operating temperature
Processors (in situ)
Examples for processors used for in-situ measurements in SiME within the SPP 2305 are:
- STM32U5xxx (Relatively low power, but offers high processing power (Cortex M33); fast, efficient ADC (2.5 MSPS at 1 mA))
- PSOC 6 CY8C63xxx (Low Power MCU, dual ARM CPU (M0+ for controlling, M4 for data processing), BT LE 5.0 subsystem, multi-channel ADC (1 mA @ 1 MSPS), programmable analog subsystems)
- BGM220S (Low Power MCU (<200nA Deep Sleep), Cortex M33, BLE 5.2, Integrated RF-Frontend+Antenna, Wakeup through RF Signal in Deep Sleep)
Methodology for design of SiME
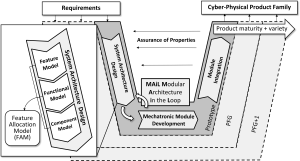
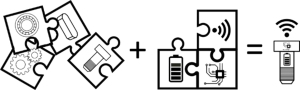
SiME can be understood as mechatronic or cyber-physical systems (CPS) due to their mechanical, electrical and information technology components. The development of mechatronic systems can be methodically supported, e.g. by the V-Model. The VDI guideline VDI2206 for the design of mechatronic systems uses the V-model as a central development tool. In the V-model, discipline-specific solutions are developed based on the requirements and checked through verification and validation activities in the form of tests and simulations. A V-model adapted to the development of modular product architectures can be seen here [46].
Low level support for development of SiME
Most methodologies for support of development are designed to support on a high level level only. Low level support for SiME as specifications for the established methodologies are needed to support development. The projects within the SPP 2305 can provide the specifications through best practices and learnings.
As an example a procedure for sensor integration into cylindrical machine elements is currently being developed. Support on a low level can include e.g. best practices on how to identify the design space for the sensors, how strain gauges can be identified and how to reproducibly apply them on a structure. Also wiring issues and temperature compensated electrical design are learnings that are provided by projects within the SPP 2305.
Modular system
The idea of a modular system is to be able to create products by combining modules. For SiME, this means being able to create application-specific system configurations of microelectronic components and modules for sensor systems for SiME with minimal effort. Depending on the ME and application, suitable components and modules are selected and configured into a compatible overall system, which is then integrated into the respective ME in a space-neutral manner without impairing the primary function.
The figure shows this schematically by equipping various ME such as a gear wheel, ball bearing, screw or feather key with an integrated sensor system and thus becoming a SiME. The sensor systems require basic modules for their functionality to fulfill their respective measuring task, suitable data processing and successful energy management.
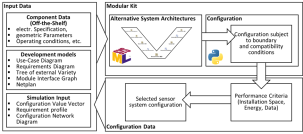
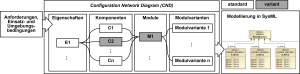
A methodical procedure for developing a configurable modular system is shown schematically here. The procedure mainly consists of a data input and two associated methods. First, the product architectures are implemented in SysML. Then, the configuration system creates a sensor system based on boundary conditions and compatibility issues. The individual product/ system variants generated on the basis of the various product architecture alternatives are then evaluated based on performance criteria.
Configuration network diagrams are created for system synthesis. The product properties are linked to the components and the components are assigned to the respective modules. The overall structure can then be implemented in SysML.
For the implementation in SysML a hierarchical structure is followe which can be accessed via package diagrams. The V-model serves as a Meta-metamodel inihibiting the metamodels and the models. The metamodels are dependency matrices which connect different model types. The models themselves represent the lowest modeling level.
In SysML, individual diagrams can be created separately, which are arranged along the V-model as shown here. Different diagram types can be used in SysML, such as requirement or block diagrams, in which the product properties, components, modules and module variants can be mapped. The individual diagrams can be linked by dependency matrices. In this case, requirements are linked to product properties, properties to components, components to modules and modules to module variants. An exemplary hierarchical requirements diagram is shown here.
In the project sensor-integrating bolt for multi-axial force measurement a modular electronics architecture realized as a flex pcb with interfaces to swap the module for data and energy transfer was developed. This enables an adaptation to different environmental settings, e.g. bright and dark environments (solar panels) or electromagnetic interferences (HF-technology).
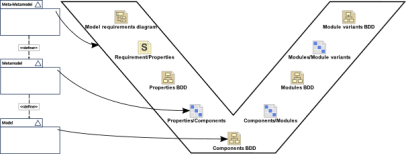
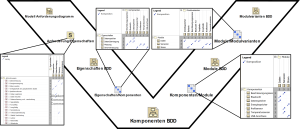
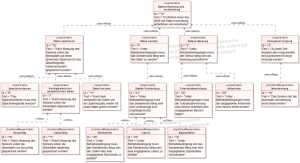
Costs of electronic components
The cost of the electronic components differs typically by their specification. By the integration of sensors, the cost of the machine element are rising. These costs can be compensated by added value of reliability and availability of the monitored machine element.
High-quality
For desired monitoring and validation of components typically high-quality sensors are used. The high-quality sensors offer typically high-sensitivity, low-noise, and high-resolution at many measurement tasks. Often the requirements on the measurement task is not known or high reproducability is required.
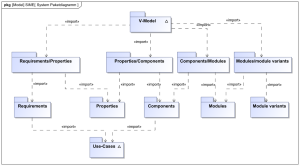
Low-quality
Low-quality sensors are widely used because of their low cost and availability by the wide use of smart devices.
Literature
- ↑ 1.0 1.1 1.2 1.3 Kirchner, E., Wallmersperger, T., Gwosch, T., Menning, J. D., Peters, J., Breimann, R., ... & Stahl, K. (2024). A Review on Sensor‐Integrating Machine Elements. Advanced Sensor Research, 3(4), 2300113.
- ↑ Welzbacher, P., Schulte, F., Neu, M., Koch, Y., & Kirchner, E. (2021). An approach for the quantitative description of uncertainty to support robust design in sensing technology. Design Science, 7, e18.
- ↑ International Organization for Standardization (2019, November 1). Calculation of load capacity of spur and helical gears (ISO 6336). Beuth.
- ↑ Knoll, E., Rothemund, M., Otto, M., Rupprecht, B., Ochs, M., Vogel-Heuser, B., Brederlow, R., & Stahl, K. (2024). Evaluation of vibration behavior at different sensing positions on gearboxes. Forschung Im Ingenieurwesen, 88(1). https://doi.org/10.1007/s10010-024-00750-6
- ↑ Binder, M., Stapff, V., Heinig, A., Schmitt, M., Seidel, C., & Reinhart, G. (2022). Additive manufacturing of a passive, sensor-monitored 16MnCr5 steel gear incorporating a wireless signal transmission system. Procedia CIRP, 107, 505–510. https://doi.org/10.1016/j.procir.2022.05.016
- ↑ 6.0 6.1 Hasenoehrl, S., Peters, J., & Matthiesen, S. (2024). Integration of Sensors for Enhanced Condition Monitoring in Polymer Gears: A Comparative Study of Acceleration and Temperature Sensors. Applied Sciences, 14(6), 2240. https://doi.org/10.3390/app14062240
- ↑ 7.0 7.1 Knoll, E., Rupprecht, B., Groppo, E., Otto, M., Vogel-Heuser, B., Brederlow, R., & Stahl, K. (2023). MODULAR EXTENSION OF FZG-GEAR TEST RIG FOR IN-SITU MEASUREMENT POSSIBILITIES. In IIAV CZECH s.r.o. (Chair), 29th International Congress on Sound and Vibration. Symposium conducted at the meeting of IIAV CZECH s.r.o., Prag.
- ↑ Peters, J., Ott, L., Dörr, M., Gwosch, T., & Matthiesen, S. (2021a). Design of sensor integrating gears: methodical development, integration and verification of an in-Situ MEMS sensor system. Procedia CIRP, 100, 672–677. https://doi.org/10.1016/j.procir.2021.05.142
- ↑ Peters, J., Ott, L., Dörr, M., Gwosch, T., & Matthiesen, S. (2021b). Sensor-integrating gears: wear detection by in-situ MEMS acceleration sensors. Forschung Im Ingenieurwesen. Advance online publication. https://doi.org/10.1007/s10010-021-00575-7
- ↑ Lau, H. Y.; Liu, K. P.; Wong, P. L.; Wang, Wen (2012): A new design of smart journal bearing based on GMM actuators. In: Industrial Lubrication and Tribology 64 (3), S. 147–151. DOI: 10.1108/00368791211218678.
- ↑ Ni, Sen (2022): Study on Mixed Lubrication Property of Planetary Gear Journal Bearing in Wind Turbine Gearbox. In: 2022 International Conference on Manufacturing, Industrial Automation and Electronics (ICMIAE). Rimini, Italy, 26.08.2022 - 28.08.2022: IEEE, S. 24–32.
- ↑ Jonuschies, Ingo (2015): Hydrodynamisch wirkende zylindrische Radialgleitlager für die Rotorwellenlagerung in Windenergieanlagen. Dissertation.
- ↑ Rolink, Amadeus; Schröder, Tim; Jacobs, Georg; Bosse, Dennis; Hölzl, Johannes; Bergmann, Philipp (2020): Feasibility study for the use of hydrodynamic plain bearings with balancing support characteristics as main bearing in wind turbines. In: J. Phys.: Conf. Ser. 1618 (5), S. 52002. DOI: 10.1088/1742-6596/1618/5/052002.
- ↑ Sauer, Bernd (2018): Konstruktionselemente des Maschinenbaus 2. Berlin, Heidelberg: Springer Berlin Heidelberg.
- ↑ Hinzen, Hubert (2022): Hubert Hinzen: Maschinenelemente/Lager, Welle-Nabe-Verbindungen, Getriebe. 5., aktualisierte Auflage. Berlin: De Gruyter Oldenbourg (De Gruyter Studium, 2).
- ↑ Althaus, Josef (1991): Eine aktive hydraulische Lagerung für Rotorsysteme (Fortschritt-Berichte VDI, Series 11, N154).
- ↑ Kurth, R.; Tehel, R.; Päßler, T.; Putz, M.; Wehmeyer, K.; Kraft, C.; Schwarze, H. (2019): Forming 4.0: Smart machine components applied as a hybrid plain bearing and a tool clamping system. In: Procedia Manufacturing 27, S. 65–71. DOI: 10.1016/j.promfg.2018.12.045.
- ↑ Santos, Ilmar F. (2011): Trends in Controllable Oil Film Bearings. In: K. Gupta (Hg.): IUTAM Symposium on Emerging Trends in Rotor Dynamics, Bd. 1011. Dordrecht: Springer Netherlands (IUTAM Bookseries), S. 185–199.
- ↑ Thielen, S., Stiemcke, Y., Sauer, B., Koch, O., Sivasothy, P., Seewig, J., Rheinländer, C., & Wehn, N. (2022). Sensorintegrierendes Maschinenelement Radialwellendichtring zur Überwachung von Betriebszustand und Schmierstoffqualität, Dresdner Maschinenelemente Kolloquium 2022, S.127-139
- ↑ Stiemcke, Y., Thielen, S., Sauer, B., Koch, O., Uebel, J., Seewig, J., Rheinländer, C., Wehn, N., & Nikolaus, K.(2024). Entwicklung eines Sensorintegrationsverfahrens zur in situ Erfassung der Kontakttemperatur von Radialwellendichtringen, Dresdner Maschinenelemente Kolloquium 2024
- ↑ 21.0 21.1 Stiemcke, Y., Thielen, S., & Koch, O. (2024). Theoretical concept for in-situ condition monitoring of rotary shaft seals using surface strain-based analysis of the deformation state. Engineering Research-Forschung im Ingenieurwesen (Preprint). URN: urn:nbn:de:hbz:386-kluedo-81078.
- ↑ Rupprecht, B., Sendlbeck, S., Vogel-Heuser, B., Brederlow, R., Knoll, E., & Stahl, K. (2023, August). Analysis of Acceleration Data Using Low-Power Embedded Devices to Detect Gear Faults. In 2023 IEEE 19th International Conference on Automation Science and Engineering (CASE) (pp. 1-6). IEEE.
- ↑ https://www.lora-wan.de/
- ↑ Rupprecht, B., Hujo, D., & Vogel-Heuser, B. (2022, August). Performance evaluation of ai algorithms on heterogeneous edge devices for manufacturing. In 2022 IEEE 18th International Conference on Automation Science and Engineering (CASE) (pp. 2132-2139). IEEE.
- ↑ Rupprecht, B., Vogel-Heuser B., Möhrle J., & Hujo D. (2024, May). Sparse Measurement Algorithm Execution Time Prediction on Heterogeneous Edge Devices for Early Stage Software-Hardware Matching. In 2024 IEEE 7th International Conference on Industrial Cyber-Physical Systems (ICPS) IEEE.
- ↑ Rupprecht, B., Vogel-Heuser, B., & Neumann, E. M. (2023, July). Measurement Methods for Software Execution Time on Heterogeneous Edge Devices. In 2023 IEEE 21st International Conference on Industrial Informatics (INDIN) (pp. 1-6). IEEE.
- ↑ Mescheder, U. (2004). Mikrosystemtechnik. 2., überarb. und erg. Auflage, Vieweg + Teubner Verlag. ISBN: 3519162563.
- ↑ Völklein, F., & Zetterer, T. (2006). Praxiswissen Mikrosystemtechnik: Grundlagen-Technologien-Anwendungen. Springer-Verlag.
- ↑ Brinkmann, B. (2012). Internationales Wörterbuch der Metrologie: Grundlegende und allgemeine Begriffe und zugeordnete Benennungen (VIM) Deutsch-englische Fassung ISO/IEC-Leitfaden 99: 2007. Beuth Verlag.
- ↑ Deutsches Institut für Normung e. V. (1995). Grundlagen der Messtechnik - Teil 1: Grundbegriffe.
- ↑ https://en.wikipedia.org/wiki/Wheatstone_bridge
- ↑ F. Herbst et al., "Multi-axis Force Sensor for Sensor-integrating Bolts," 2022 IEEE Sensors, Dallas, TX, USA, 2022, pp. 1-4, doi: 10.1109/SENSORS52175.2022.9967220
- ↑ Stroppe, H., & Schiebold, K. (2011). Wirbelstrom-Materialprüfung: ein Lehr-und Arbeitsbuch für Ausbildung und Prüfpraxis; mit 29 Tabellen. Castell-Verlag.
- ↑ Gansel, R., Quanz, M., Lohrengel, A., Maier, H. J., & Barton, S. (2024). Qualification of Austenitic Stainless Steels for the Development of Load-Sensitive Material Sensors. Journal of Materials Engineering and Performance, 1-13.
- ↑ Rosset, S., & Shea, H. R. (2016). Small, fast, and tough: Shrinking down integrated elastomer transducers. Applied Physics Reviews, 3(3)
- ↑ Mathias, J., Kloberdanz, H., Engelhardt, R., & Birkhofer, H. (2010). Strategies and principles to design robust products. In DS 60: Proceedings of DESIGN 2010, the 11th International Design Conference, Dubrovnik, Croatia (pp. 341-350).
- ↑ Kiziroglou, M. and E. Yeatman. Materials and techniques for energy harvesting. In: Functional Materials for Sustainable Energy Applications, 541–72. Elsevier.'https://doi.org/10.1533/9780857096371.4.539, 2012.
- ↑ Kishore, R. A., & Priya, S. (2018). A Review on Low-Grade Thermal Energy Harvesting: Materials, Methods and Devices. Materials (Basel, Switzerland), 11(8).
- ↑ Snyder, G. J., & Toberer, E. S. (2008). Complex thermoelectric materials. Nature materials, 7(2), 105–114.
- ↑ Abdal-Kadhim, A. M., & Leong, K. S. (42017). Application of thermal energy harvesting from low-level heat sources in powering up WSN node. In 2017 2nd International Conference on Frontiers of Sensors Technologies (ICFST) (pp. 131–135). IEEE.
- ↑ Attivissimo, F., Lanzolla, A. M. L., Passaghe, D., Paul, M., Gregory, D., & Knox, A. (52014). Photovoltaic-thermoelectric modules: A feasibility study. In 2014 IEEE International Instrumentation and Measurement Technology Conference (I2MTC) Proceedings (pp. 659–664). IEEE.
- ↑ Bhattacharya, M., Ranjan, M., Kumar, N., & Maiti, T. (2021). Performance Analysis and Optimization of a SnSe-Based Thermoelectric Generator. ACS Applied Energy Materials, 4(8), 8211–8219.
- ↑ Gou, X., Xiao, H., & Yang, S. (2010). Modeling, experimental study and optimization on low-temperature waste heat thermoelectric generator system. Applied Energy, 87(10), 3131–3136.
- ↑ Niu, X., Yu, J., & Wang, S. (2009). Experimental study on low-temperature waste heat thermoelectric generator. Journal of Power Sources, 188(2), 621–626.
- ↑ Quanz, M., Gansel, R., Barton, S., Lohrengel, A. (2023). Energy Harvesting in rotierenden Maschinenelementen. In Mitteilungen aus dem Institut für Maschinenwesen der Technischen Universität Clausthal Nr. 48.
- ↑ Küchenhof, J., Berschik, M. C., Heyden, E., & Krause, D. (2022). Methodical support for the new development of cyber-physical product families. Proceedings of the Design Society, 2, 495-504.